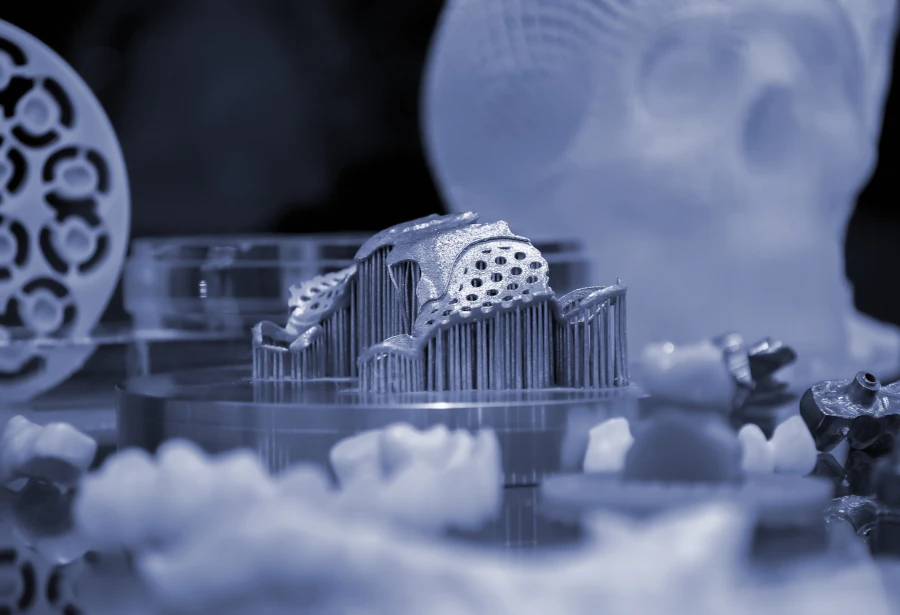
Additive Manufacturing Support Structures: What You Need to Know
The invention of additive manufacturing (AM) ushered in a new era of manufacturing possibilities. AM technology enables us to create previously unimaginable parts, featuring complex dimensions and angles, with unprecedented speed and precision.
However, the nature of the additive manufacturing process, in which material is added layer-by-layer, often means that parts require support to manage internal pressure–essentially, the force of gravity–during the print. Without that support, additive layers can’t be held up by the material around them and collapse, causing the print to fail. You often need to add support structures into your AM part design to address this challenge.
To ensure you maximize the potential of your part for speed, quality, and cost, it’s important to understand support structures and how they should be integrated into your additive manufacturing project.
What Is a Support Structure in Additive Manufacturing?
In additive manufacturing, a support structure is any material used to provide structural support to an overhanging or otherwise unsupported portion of a printed part during the build process.
Why Use Support Structures?
Support structures in AM act as a scaffold, providing stability and preventing objects from shifting or collapsing. Without support structures, parts would be more likely to warp or collapse, resulting in an unusable final part. Supports also help improve the accuracy of the printing process by keeping the object in place. As a result, they play an essential role in the successful production of parts using additive manufacturing.
Common Types of Support Structures
Many types of support structures can be used in additive manufacturing, each with its own advantages and disadvantages. Some common types of support structures used in AM are:
- Breakaway Supports
- Lattice Supports
- Soluble Supports
Breakaway Supports
Breakaway supports are one of the most common types of support structures used in additive manufacturing. Breakaway supports are made from materials that can easily be removed by hand, such as wax.
The advantage of using breakaway supports is you can easily remove them from your parts without damaging them. However, breakaway supports are not well-suited for supporting large or complex geometries, and they’re not reusable like some other support types.
Lattice Supports
Another type of support structure commonly used in additive manufacturing is lattice supports. Lattice supports are created using honeycomb- or lattice-like structures that are a cost-effective way of providing mechanical strength while still being relatively easy to remove.
An advantage of using lattice supports is that they can be custom-tailored to fit the exact geometry of the part being printed. However, lattice supports can be expensive to produce and they’re not well suited for supporting very large or complex parts.
Soluble Supports
The third type of support structure that is often used in additive manufacturing is soluble supports. Soluble supports are made from materials that can be dissolved in water or other chemicals after printing is complete.
The advantage of using soluble supports is they can be easily removed from the finished part without damaging it. However, soluble supports are not well suited for supporting large or complex geometries and require careful planning to ensure the finished part will not be damaged during the removal process.
AM Technologies and Support Structures: A Brief Overview
Almost all 3D printing technologies require support structures to some degree. Let’s take a closer look at how each additive manufacturing method differs in using supports:
Binder Jetting
During the binder jetting process, a binding agent is selectively deposited onto a powder bed, bonding the areas together to form a solid part, one layer at a time.
One major advantage of binder jetting over other types of additive manufacturing is that binder jet parts are supported by loose powder in the build chamber, often eliminating the need for dedicated support structures.|
Powder Bed Fusion (DMLS, SLM, EBM)
Parts created with powder bed fusion technologies, such as direct metal laser sintering (DMLS), require supports to anchor to the base plate and reduce the effects caused by residual stress. Supports are added between the bottom of the printed part and the print bed, where the most residual stress is found. This can also minimize thermal distortion by drawing heat away from the part, making cracking, sagging, shrinkage, delamination, and warping less likely.
Material Jetting
Supports are required for overhangs when using material jetting technology. These supports are often created out of materials that are easily removed by using pressurized water or submerging them in an ultrasonic bath.
Fused Deposition Modeling (FDM)
During Fused Deposition Modeling (FDM), parts are made by extruding heated filament, layer by layer. As the layers cool, they solidify and bond with each other. Dissolvable supports, such as High-Impact Polystyrene (HIPS) and Polyvinyl Alcohol (PVA) are often used with FDM technology. Using dissolvable supports has the benefit of being hands-free and doesn’t require further post-processing to remove marks left by the supports.
Direct Energy Deposition (DED)
Direct Energy Deposition is an additive technology that melts and fuses materials to create a part. Similar to powder bed fusion, parts printed using DED require support structures to ensure stability, printability of complex features, and thermal dissipation.
Support removal can be trickier than polymer-based processes and cutting tools are typically required.
Stereolithography (SLA)
Stereolithography technologies work by solidifying liquid resins with a light source. Support structures are required to attach parts to the print bed and to prevent warping. To save material, thin supports that only slightly touch the part are used. Removing supports can leave prints on the final part, so sanding is necessary if you desire a smooth surface finish.
SLA is preferred for applications where a smooth surface finish is required, such as molds, visual prototypes, and hearing aids. To ensure a smooth surface finish, design your part so the forward-facing areas of your print aren’t in contact with support structures.
Designing for Excellence
You need to keep a number of factors in mind when designing for additive manufacturing, including support structures. To help you navigate the intricacies involved in DFAM (design for additive manufacturing), partnering with a manufacturer well-versed in additive technologies can be helpful.
To learn more about additive manufacturing, check out our blog.