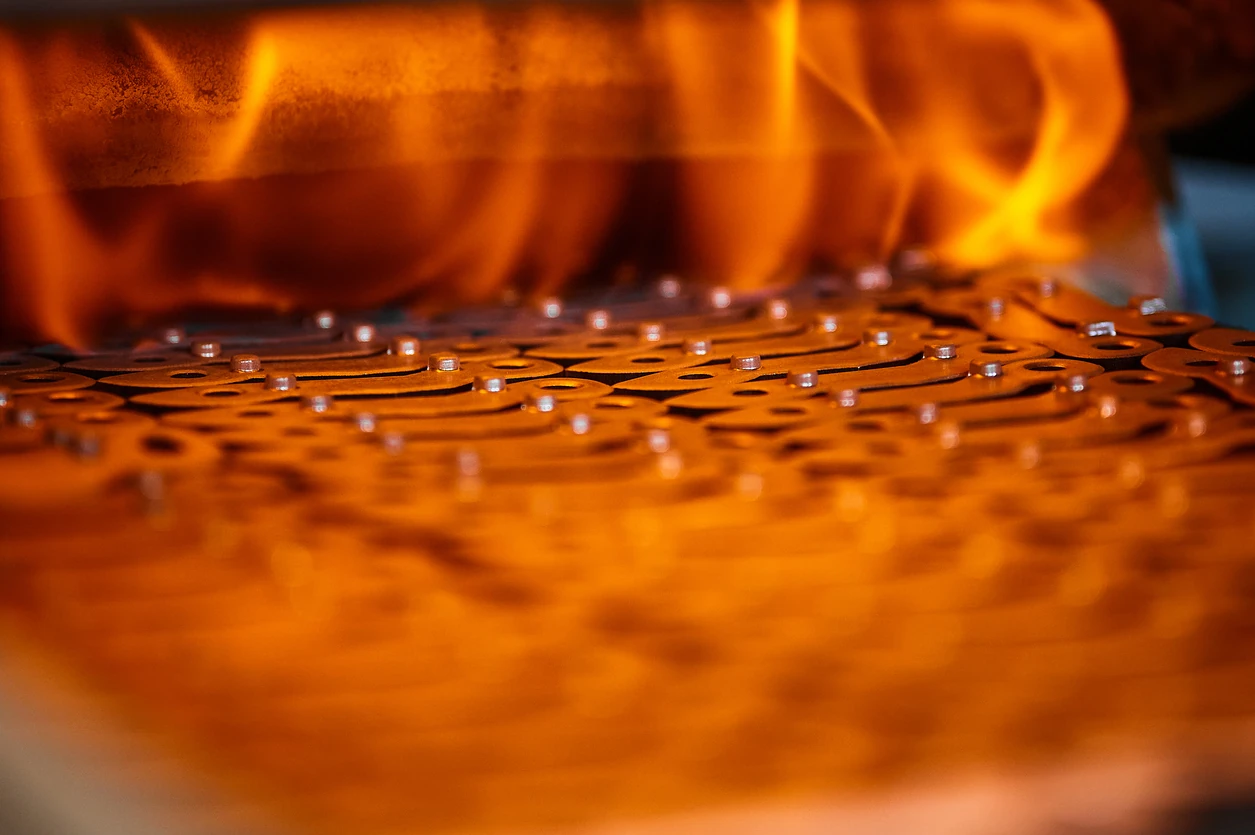
The Advantages & Disadvantages of Powder Metallurgy
New technology is breaking ground. Manufacturers are mass-producing like never before.
The latest news highlights how new technology is changing the way we produce products. While this new tech is incredible, sometimes the tried and true methods are the way to go.
Powder metallurgy (PM) isn’t the latest and greatest advancement in technology by any means, it’s one of the oldest manufacturing methods.
Why is the powder metallurgy process still used today?
That’s easy – it works.
In this blog, we’ll discuss the advantages and disadvantages of using traditional powder metallurgy as well as when to choose PM over other methods.
What is Powder Metallurgy?Before digging into the pros and cons of powder metallurgy, it’s important to understand what this manufacturing method is and how it works. Powder metallurgy is a process using heat and compression to create components from powdered metal. This process can be broken down into four steps:
|
The Advantages of Powder Metallurgy
With many advanced methods of production to choose from, why are manufacturers still opting for powder metallurgy?
There are many reasons. The main five advantages of powder metallurgy are:
- Waste materials & costs are minimized
- Ability to alter final properties
- Producing precise, complex parts
- Skipping the finishing process
- Applying automation
1. Waste Materials & Costs are Minimized
Nearly every manufacturing process strives to reduce waste and remain cost-effective. Powder metallurgy does both. PM is an environmentally friendly way to mass produce parts using more than 97% of the starting material, which other methods can’t match.
As mentioned above, the first step in the powder metallurgy process is creating metal powder. If there is any unused powder, it can be reused in another cycle, lowering waste right from the start of the process.
During the compaction step in the powder metallurgy process, the components are pressed to their final size, so there isn’t any excess scrap metal to remove in finishing. While PM only loses 1-5% of metal, other production methods can lose up to 80% of the metal. With less metal waste, cost savings automatically increase.
2. Ability to Alter Final Properties
In powder metallurgy, four factors affect the properties of the final component:
- Powder type
- Powder’s particle size
- Amount of binder
- Sintering conditions
When choosing the powder type, use multiple metals to create alloys unique to each part. The combination of alloys with binders determines the pH level, viscosity, and filtration level of the component.
The remaining factors affect the part’s performance and final properties, such as its porosity, hardness, and stress performance.
The ability to alter the final part’s properties is unique to powder metallurgy, and one of the reasons the process is still used today.
3. Producing Precise, Complex Parts
In addition to the specific properties PM offers, the process produces highly accurate and precise parts.
Because powder particles are easily controlled, they can be formed into the desired shape quickly and easily.
4. Skipping the Finishing Process
Since parts are near-net shape after sintering, finishing isn’t necessary. Skipping the finishing step can benefit in three ways:
- Saving costs by removing the need for additional materials
- Shortening the time to market by producing faster than processes with a long finishing step
- Maintaining consistency by having the same surface finish
With highly precise parts that don’t require finishing, the powder metallurgy process is advantageous to industries looking to cut down on time and costs, such as the automotive industry.
5. Applying Automation
Powder metallurgy is a cost-effective and consistent process – but automation takes it to the next level. Automation in powder metallurgy can be applied to the process from beginning to end, starting with the blending and compaction stages.
Automated powder blenders precisely measure powder and accurately mix them. From there, the powders can automatically be compacted by hydraulic or mechanical presses, resulting in a consistent density every time.
Once the part moves to the sintering phase, automated sintering furnaces can be temperature-controlled and regulated to ensure the highest quality.
Throughout the entire powder metallurgy process, automated inspection systems perform quality control. These systems detect any error or defect that may occur before they even happen. Quickly correcting issues saves time and costs in the long run.
Disadvantages of Powder Metallurgy
No process is perfect. While PM has its advantages, there are three disadvantages of powder metallurgy:
- Limited by size & shape
- Costly ineffective in small quantities
- Density varies based on compaction
1. Limited by Size & Shape
While powder metallurgy efficiently creates precise parts, producing complex, large parts is difficult. The fluidity of powder causes restrictions, resulting in parts with simple structures.
Additionally, the size of the final component is limited to the capacity of the press. Parts produced by PM are limited to 20 kilograms or less, much smaller than other manufacturing methods.
Pro Tip: If you’re looking for a production method to produce complex, intricate parts, metal additive manufacturing is a solution!
2. Cost Ineffective in Small Quantities
When mass-producing with powder metallurgy, the process is cost-effective. When producing in small batches, the costs can outweigh the profit.
Powder metallurgy equipment is relatively costly upfront. Presses, sintering furnaces, and powder mixing machines must be purchased before you even begin. Additionally, labor, tooling, and material costs add up quickly when producing in small quantities.
How does mass production lower these costs?
When mass-producing, the cost is spread over a large number of components.
3. Density Varies Based On Compaction
In powder metallurgy, achieving a consistent density throughout the part can be challenging. The density of parts can vary for many reasons:
- Particle size
- Shape
- Cracks
- Defects
- Powder distribution
During the compaction step of the powder metallurgy process, pressure is applied to achieve increased density. If the level of pressure varies, even slightly, the density between parts can be completely different.
When is Powder Metallurgy Right for the Job?
If you’re looking for a manufacturing process, powder metallurgy may be the perfect fit if you’re looking for a way to:
- Mass-produce parts
- Skip the finishing step
- Maintain a high level of precision
- Produce using a variety of materials
Powder metallurgy is an efficient process if you’re highlighting its advantages. Taking the disadvantages into consideration is equally important when choosing the best production method.
Powder Metallurgy – A Tried & True Method
While powder metallurgy isn’t the newest – or flashiest – manufacturing process, it has certainly earned its place as a viable & reliable option for part fabrication. Even in spite of its disadvantages, PM remains a tried, trusted, and true method for those looking to bring efficiency and cost control to large-run projects.
Ready to Get Started?
Weighing your options can be difficult – consult with one of our specialists to ensure you’re making the correct decision.