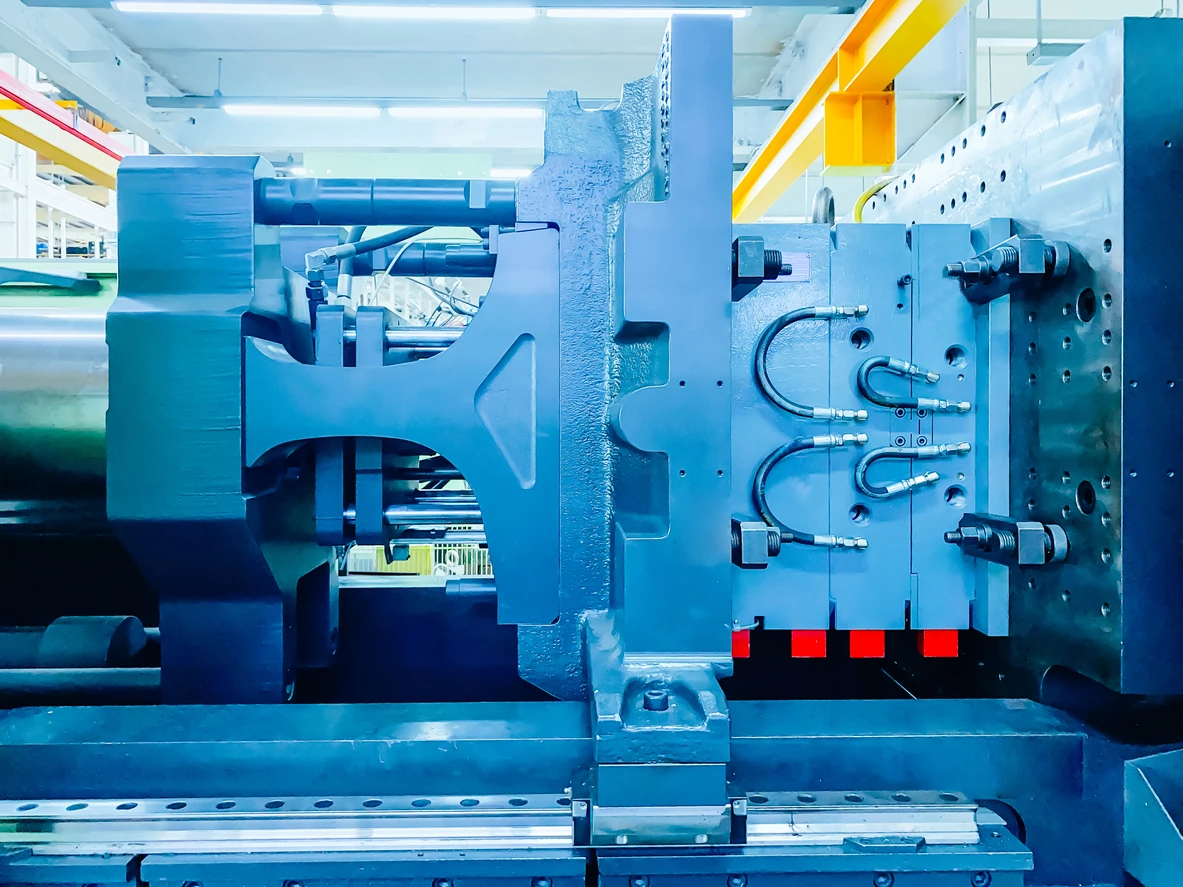
Metal Injection Molding Services in Mass Production: When MIM is Best
Manufacturing is continuously evolving with new technology. Metal injection molding (MIM) isn’t the latest method or the newest technology. In fact, it’s been around for quite some time.
Despite recent technology and innovations, metal injection molding services are still used for mass production in manufacturing.
How Does Injection Molding Work?
Before getting into why metal injection molding for mass production is best, it’s important to first understand how the process works.
The MIM process can be broken down into four steps:
- Preparing the feedstock by mixing metal powder with binders
- Injecting the mold cavity with the feedstock
- Removing the binder through debinding processes
- Sintering in a high-temperature furnace to heat and remove the binders
Overall, the process is straightforward, which is only one of the several reasons to choose MIM for large-scale production.
5 Reasons to Choose Metal Injection Molding Services for Mass Production
When deciding which manufacturing process is best for mass production, consider the following:
- Customizable
- Durability & flexibility
- Simplified mass production
- Tight tolerances, even in high volumes
- Increased ROI
1. Customizable
The MIM mold design can easily be changed to produce different size parts and increase design complexity. Additionally, adding various attachments to your metal injection molding machine allows you to add different features and alter the final surface texture.
Not only can the part’s structure be changed, but the color can too by adding pigment or dye to the material.
2. Durability & Flexibility
In manufacturing, sometimes you have to decide between durability and flexibility. With metal injection molding, no compromise is necessary.
MIM combines the durability of producing with metal, with the flexibility of plastic injection molding.
3. Simplified Mass Production
Think of an ice cube tray. To make multiple ice cubes, just fill the tray with water, put it in the freezer, and you’ll have 10+ ice cubes in no time. If your tray only has one spot to put water, you’ll only have one ice cube.
Clearly, having a tray with 10+ spots is more efficient than just one. Similarly, if your MIM mold only has one place for material, it’s much less efficient than designs with many.
Metal injection molding for mass production can be simplified by only changing the mold design. If your mold has several places to fit material, you can produce many parts at once.
4. Tight Tolerances, Even in High Volumes
The MIM process boasts tolerances of ±0.3% to ±0.5% of the nominal dimension. These tolerances aren’t achieved with any manufacturing method, MIM is superior.
While several factors such as part geometry, materials, and feedstock preparation can affect the final component, the precision of metal injection molding ensures tight tolerances are achieved.
5. Increased ROI
Even though MIM carries a higher upfront investment, your ROI will increase significantly when mass producing.
The more parts you produce, the faster your ROI increases.
If you’re only creating one part at a time, generating a profit will be difficult. Using MIM molds with multiple components will quickly increase profit.
Metal Injection Molding in Action
With its ability to produce small, intricate parts in high volumes, the process is widely used in industries such as the medical field, firearms, and the automotive industry.
Medical – The demand for intricate yet durable surgical tools is high in the medical field. Medical injection molding meets and exceeds strict medical standards, while also meeting the demand for products.
Firearms – The firearm industry has a focus on safety and efficiency. Metal injection molding meets both those requirements. MIM is frequently used to produce mass quantities of hammers, triggers, levers, and more in the firearm industry.
Automotive – MIM produces several different components found in vehicles, such as shift levers, electrical connectors, power steering systems, and various sensors.
Unleash the Possibilities with Metal Injection Molding Services
Metal injection molding isn’t the latest and greatest innovation or the newest technology.
However, metal injection molding services hold their place in mass production as a cost-effective way to produce small parts at a high volume.
Ready to Get Started on Your Next Project?
As mentioned above, the MIM process is straightforward, but metal injection molding for mass production can be a bit more in-depth and complex.
Reach out to one of our specialists to help guide you through getting started with MIM.