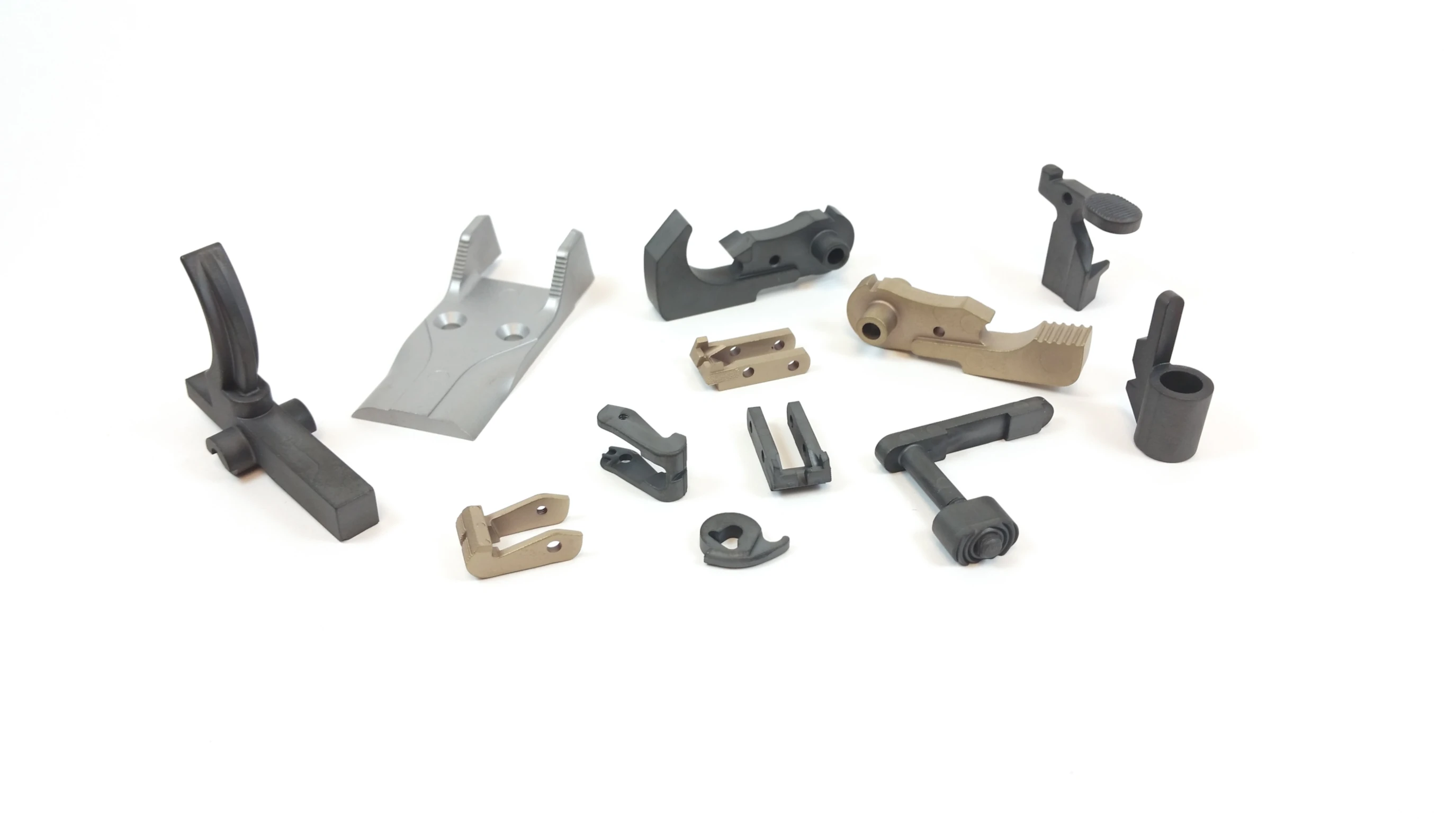
Metal Injection Molding in the Defense Industry
Imagine trying to manufacture a firearm with inaccurate parts. The firearm would most likely not work, but it could also malfunction and be dangerous to the operator and those around.
It’s essential to have the most precise and accurate parts available when producing firearms to ensure safety and optimal performance. The solution – metal injection molding.
Metal injection molding in the defense industry has rapidly grown due to its ability to create small, complex parts in mass volumes. In this blog, we’ll dive into the details of MIM and firearms.
What is Metal Injection Molding?
We’ll start with the basics. MIM has the ability to produce highly complex, intricate parts yet the process is quite simple. If you’ve worked with plastic injection molding, it’s the same concept.
Forming the Feedstock
The metal injection molding process starts with fine metal powder and binders being mixed to form a feedstock. The mixture of powder and binder allows the material to flow in the injection molding process, similar to traditional polymer injection molding.
Molded into Shapes
Then, the feedstock is placed into an injection molding machine, where it’s heated and injected into a mold cavity under high pressure. The ‘green’ part is then allowed to cool and removed from the mold so the process can be repeated.
Binder Removal
The part is now ready to move onto the debinding, or binder removal process. The majority of debinding takes place prior to sintering, however, there is enough remaining binder to keep the part intact while entering the furnace. After debinding, the part will be semi-porous, which allows the remaining binder to escape during the sintering process.
Sintering
Throughout the sintering process, heat is applied to the feedstock. Once it nears melting point, the binders start to liquefy and evaporate. Once all of the binders have been released, the component is heated, where it shrinks, transforming into a dense solid.
With this repeatable process and the ability to produce intricate parts in a variety of metals, metal injection molding exceeds expectations in production.
Advantages of MIM in Firearms
Most internal and critical firearms components are manufactured via metal injection molding.
Why is MIM the preferred method?
The defense industry has adopted metal injection for two main reasons – volume and cost.
Metal injection molding has the ability to produce many highly engineered parts at once, resulting in a lower cost per component than traditional machining.
While MIM is primarily used because of volume and cost, some additional benefits include:
- The ability to create small-medium sized parts
- A wide variety of materials available
- Tight tolerances to ensure proper design
- Creating complex, net-shape designs without the need for additional secondary operations
1. Ability to Create Small-Medium Sized Parts
Metal injection molding specializes in intricate designs even in small parts. When producing firearms, this capability is essential.
2. A Wide Variation of Materials to Choose From
With MIM, there’s a wide range of metal powders and binders to choose from with nearly an endless amount of alloy options. This allows for customization of the final part’s mechanical properties.
3. Tight Tolerances to Ensure Proper Design
Metal injection molding offers tight tolerances ±0.3% to ±0.5% of the nominal dimension, which is crucial when designing firearms.
4. Creating Complex Designs Without Requiring Secondary Operations
Metal injection molding has the ability to create complex designs – without post-processing. Since post-processing isn’t necessary, the cost of additional machines and equipment isn’t required.
Applications of MIM in the Defense Industry
As mentioned before, metal injection molding is the most widely used process when manufacturing for the defense industry. The most common components produced by MIM include:
- Fire Control Group Components (this includes Triggers, Hammers, Sears, Sear Housings, Disconnectors, etc.)
- Magazine Catch and Lock components
- Fire Suppression
- Sights and Sight Plates
- Stock Components and Accessories
Pro Tip: If you’re considering using metal injection molding to produce firearms, it’s critical to work with an expert that has industry experience.
Metal Injection Molding Materials for the Defense Industry
It’s no secret that firearms need to be incredibly durable and reliable. One of the ways to ensure high strength and durability of the final component is with the material selection. In metal injection molding for the defense industry, there are three materials commonly used:
- Stainless steels
- Low alloy steels
- Tool steels
Stainless Steels
The metal injection molding process itself yields high-density parts. When the MIM process is combined with stainless steel, the parts manufactured have notable strength and ductility.
Additionally, stainless steel is corrosion-resistant – which is perfect for components that need to withstand harsh environments.
Low Alloy Steels
Low alloy steels are carbon steels that reach their final properties after heat treatment. The inherent mechanical properties of post-heat treatment ensure high strength and the ability to withstand high stress and/or impact. Low alloy steels are some of the most commonly used materials in the defense industry, especially for MIM.
Tool Steels
Tool steels are resistant to abrasion and can withstand high temperatures. These are excellent for components that need to maintain their shape under heavy use or high stress.
The Future of MIM
It's no secret that firearms require safety measures and optimal performance. With the solution of metal injection molding in the defense industry, precision and accuracy requirements will be met.
Due to the excellent capabilities of injection molding, MIM is becoming growingly popular in the defense industry and doesn't seem to be slowing down. If you're curious about MIM and want to learn more about the process, reach out to our highly-experienced team today.