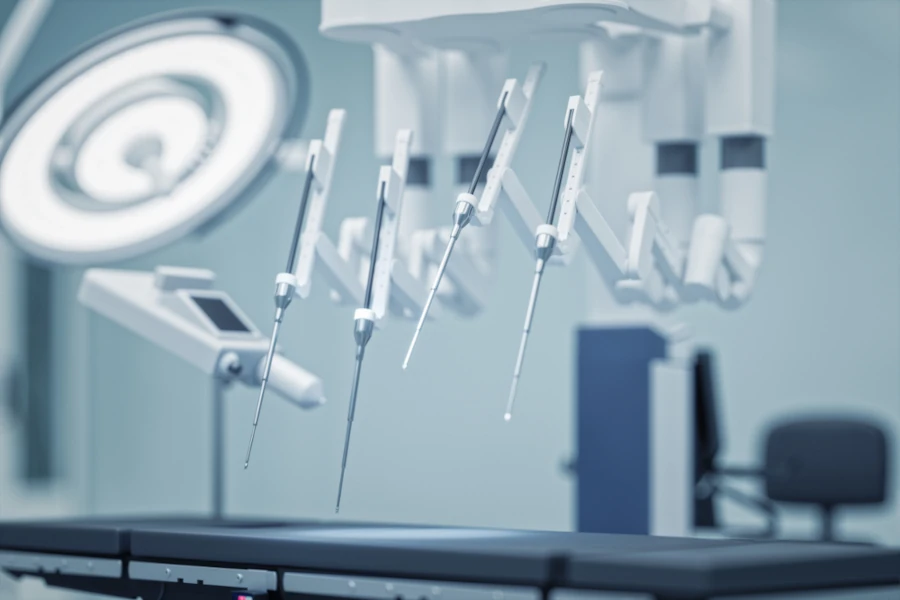
Metal Injection Molding: Transforming the Medical Industry
The medical industry has always been at the forefront of adopting innovative technologies to enhance patient care. One such breakthrough is the integration of metal injection molding (MIM) into the production of medical devices, surgical instruments, and surgical tools. The technique not only enhances performance and reliability but also fosters cost-efficiency, elevating the production of medical equipment to new heights.
The Power of MIM
MIM is a metalworking process by which finely powdered metal is mixed with a binder material to create a “feedstock” that’s then shaped and solidified using injection molding. One major advantage of MIM is its ability to shape complex geometries that are difficult to achieve with traditional metalworking processes.
Moreover, MIM can deliver intricate, high-strength parts in large volumes, providing excellent mechanical properties, tight tolerances, and a broad selection of materials. These unique attributes make it a go-to technology for numerous industries, notably the medical sector.
Revolutionizing Medical Devices
MIM’s versatility facilitates the fabrication of medical devices, often required in many shapes, sizes, and designs. MIM enables the production of parts with superior strength and intricate designs, such as internal channels or undercuts, which would otherwise be challenging or cost-prohibitive to produce using traditional methods.
Examples of MIM applications in medical devices include components for drug delivery devices, orthopedic implants, and parts for minimally invasive surgical (MIS) devices. MIM can meet the demand for precise, biocompatible, and high-performance parts necessary for these critical applications.
Advancing Surgical Instruments
MIM has also had a significant impact on the production of surgical instruments. The requirement for precise, miniaturized, and complex components has grown substantially with the advent of advanced surgical techniques like laparoscopic surgery.
Due to its ability to maintain dimensional accuracy and tight tolerances, MIM is well-suited to produce complex components, even when creating highly complex shapes. Furthermore, MIM’s efficiency in mass production allows for the cost-effective fabrication of surgical instruments like scalpels, clamps, and scissors, resulting in affordable, high-quality tools that ultimately benefit patient care.
Enhancing Surgical Tools
In the realm of surgical tools, MIM's benefits extend further. The process can mold stainless steel, titanium, and other biocompatible metals into intricate geometries with high strength and endurance. These properties are valuable in surgical tools such as drill bits, endoscopic tool components, and other specialized surgical tools.
Moreover, the design flexibility provided by MIM allows for innovation in surgical tool production, enabling the development of tools tailored to specific surgical procedures or patient demographics.
Future Outlook
MIM has made impressive strides in the medical industry, but the journey doesn’t stop here. The next frontier lies in integrating additive manufacturing (MAM) with MIM. Combining MIM and MAM may unlock further design possibilities, allowing for more complex, custom, and patient-specific devices and tools.
MIM - A Game Changer in Medical Technology
The adoption of metal injection molding in the medical industry marks a significant shift in the production of medical devices, surgical instruments, and surgical tools. Through the provision of complex, high-quality, and cost-effective components, MIM has solidified its place as an invaluable technique in the advancement of medical technology. As we continue to push the boundaries of medical science, techniques such as MIM will undoubtedly play an instrumental role in the evolution of patient care.
Want to learn more about metal injection molding? Check out our blog.