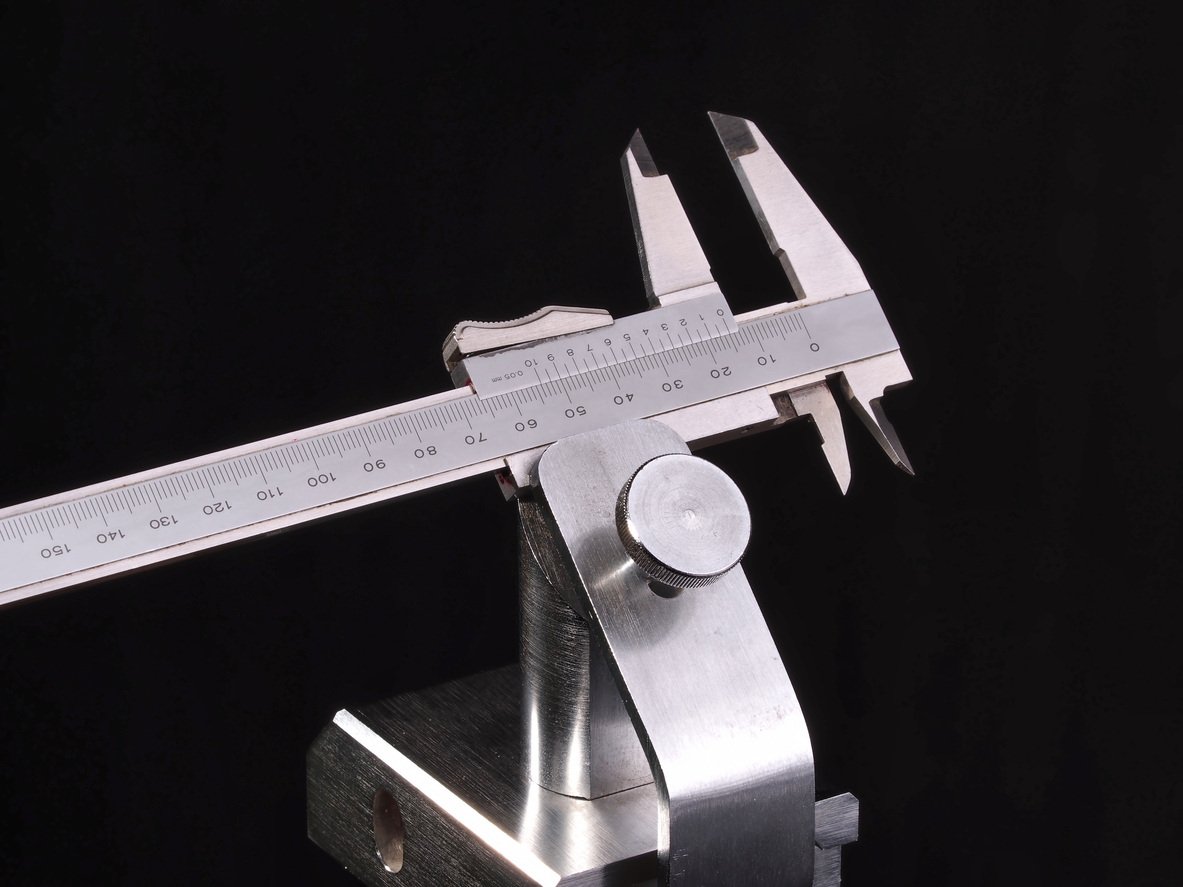
What Engineers Need to Know About Tolerances and Dimensional Control in Stainless Steel Sintering
Regarding precision components, a part is only as good as its tolerances. In stainless steel sintering, dimensional control is both a science and an art; one influenced by everything from material composition to post-sintering processes. Whether designing tight-tolerance parts or specifying fit and function in an assembly, understanding stainless steel sintering tolerances is key to predictable performance.
Why Tolerances Matter in Sintered Components
In powder metallurgy, tolerances define how closely a part’s final dimensions match its intended design. The sintering process inherently involves shrinkage, which can vary depending on the material and geometry. Managing sintering tolerances means managing those variables to achieve consistent, repeatable parts.
While stainless steel is an excellent choice for corrosion resistance and strength, it adds its own complexities to dimensional control. Understanding these nuances upfront helps avoid redesigns and delays later in the process.
Factors that Influence Stainless Steel Sintering Choices
Several variables influence how precisely a stainless steel part holds its shape during sintering, each playing a role in final dimensional accuracy:
- Material properties and powder characteristics
- Compaction pressure and green density
- Sintering temperature and atmosphere
- Part geometry and wall thickness
- Post-sintering operations
1. Material Properties and Powder Characteristics
The particle size, shape, and distribution of stainless steel powders significantly affect dimensional change during sintering. Finer particles may provide a better surface finish but can also lead to more shrinkage. Alloy content also plays a role – certain grades of stainless steel (like 316L vs. 17-4 PH) behave differently under the same conditions.
2. Compaction Pressure and Green Density
How the powder is compacted in the die influences the uniformity of the “green” (pre-sintered) part. Uneven green density leads to uneven shrinkage during sintering. Higher compaction pressures can reduce porosity and lead to better dimensional consistency, but also increase tooling wear and costs.
3. Sintering Temperature and Atmosphere
Sintering stainless steel typically requires high temperatures (often above 2100°F / 1150°C) in a controlled atmosphere. Minor variations in temperature or atmosphere (e.g., hydrogen vs. nitrogen) can cause subtle shifts in dimensional change. Maintaining tight process control is essential to achieving consistent steel sintering tolerances across batches.
4. Part Geometry and Wall Thickness
Complex geometries or varying wall thicknesses can make dimensional control more challenging. Thin-walled sections are prone to distortion, while thick sections may shrink unevenly. Design for sintering means thinking beyond the end dimensions and considering how each feature behaves during every stage of the process.
5. Post-Sintering Operations
To meet tighter metal sintering tolerances, many parts undergo secondary operations like sizing, machining, or heat treatment. However, it adds cost and must be accounted for in the design.
Typical Tolerances in Stainless Steel Sintering
As a general guide, sintered stainless steel parts without secondary sizing can typically achieve dimensional tolerances of ±0.3% to ±0.5% of the nominal dimension. For example:
- A 20 mm feature may have a tolerance range of ±0.06 mm to ±0.10 mm
- With coining/sizing, tolerances as tight as ±0.025 mm may be achievable
- Secondary machining (lathe machining, grinding, honing) for tolerances tighter than ±0.025 mm
Tolerances will vary depending on part size, geometry, and production volume, so early collaboration with your sintering partner is essential for optimizing design and cost.
Designing for Dimensional Control
To get the most out of stainless steel sintering, keep the following tips in mind during the design phase:
- Avoid sharp transitions and large differences in wall thickness.
- Use fillets to reduce stress concentration and distortion.
- Discuss critical dimensions with your manufacturing partner. Some features may need to be machined post-sintering to meet ultra-tight specs.
- Design features to be compatible with sizing operations when higher precision is required.
Putting It All Together: Designing with Tolerances in Mind
Understanding metal sintering tolerances is crucial to successful part design and production. While stainless steel presents unique challenges, careful control of materials, compaction, sintering, and post-sintering steps makes it possible to achieve the precision required for even the most demanding applications.
If dimensional stability and material performance are critical to your project, our sintering experts are ready to support you from design through full-scale production.