Building an Additive Manufacturing Business Case
How to Build an Additive Manufacturing Business Case
Metal additive manufacturing (MAM) technology is rapidly advancing, offering manufacturers new opportunities to create complex and customizable parts. While it can be challenging to make the case for investing in metal AM operations, with the right analysis and understanding of potential cost savings and benefits, you can develop a business case that makes sense for your organization.
Below is an overview of the basic steps on how to build a metal additive manufacturing business case to help your company to make informed decisions regarding investments.
Step One: Identify the Need for Metal AM
When building an additive manufacturing business case, it’s important to identify which current and future parts will benefit most from additive manufacturing. Additionally, you should look to future products and potential product enhancements that could benefit from AM in order to maximize your investments.
By taking a comprehensive approach, you can ensure you’re making the most out of your resources when investing in metal additive manufacturing.
Which Parts Benefit Most from Metal Additive Manufacturing?
When deciding on a list of possible parts to highlight, you should keep the freedom of design and performance enhancements Metal AM offers in the forefront of your mind.
Metal additive manufacturing is ideal for the following:
• Complex Geometries |
• Part Consolidation |
• Durability Improvements |
• Performance Enhancements |
• Weight Reductions |
• Customization |
• Prototypes |
• Niche Products |
• Low or High-Volume Parts |
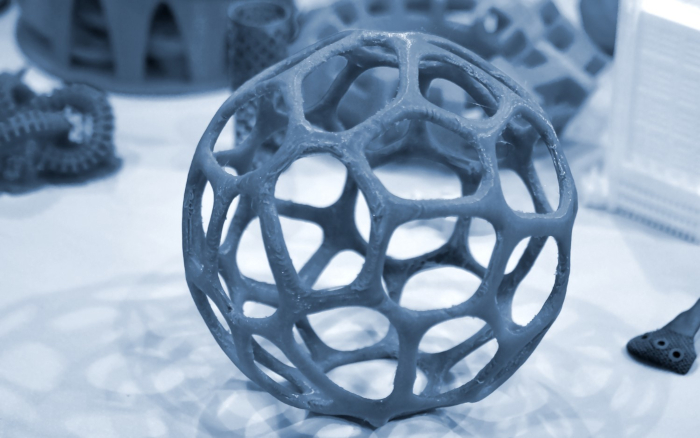
Developing an accurate cost model for additive manufacturing investments is key to understanding the potential returns from the technology. Analyze all the associated expenses that come with manufacturing those parts with your current manufacturing method versus metal additive manufacturing.
You should account for both short-term and long-term costs when building your model, including but not limited to*:
- Upfront expenses associated with installing hardware and software solutions, as well as personnel training, consulting services, and IP licensing agreements.
- Operational costs related to energy consumption & resource efficiency during production.
- Maintenance and repair costs, such as personnel labor, parts replacement, and software updates.
- Taxes & duties when selling printed parts overseas.
- Short-term cost savings from reduced production time, improved part quality with fewer defects, and increased flexibility with customizable parts.
- Long-term benefits (such as customer satisfaction or faster time-to-market capabilities) due to decreased lead times on projects and higher prices for products produced with metal AM. This is due to customizability and/or enhanced design features offered by additively manufactured components.
*While we’ve outlined the main steps in creating a business case model for in-house additive manufacturing, it’s important to note that partnering with a manufacturer with additive capabilities already in place gives you all the benefits of additive manufacturing, without the initial expensive start-up costs (machinery, training, etc.).
Cost Savings
Demonstrate how additive manufacturing can yield cost savings. A key advantage of AM technologies is that it eliminates the need for tooling and multiple setups associated with conventional manufacturing methods. By showcasing this cost-savings potential directly in your business case model, you can illustrate how AM has the potential to reduce overhead costs significantly over time.
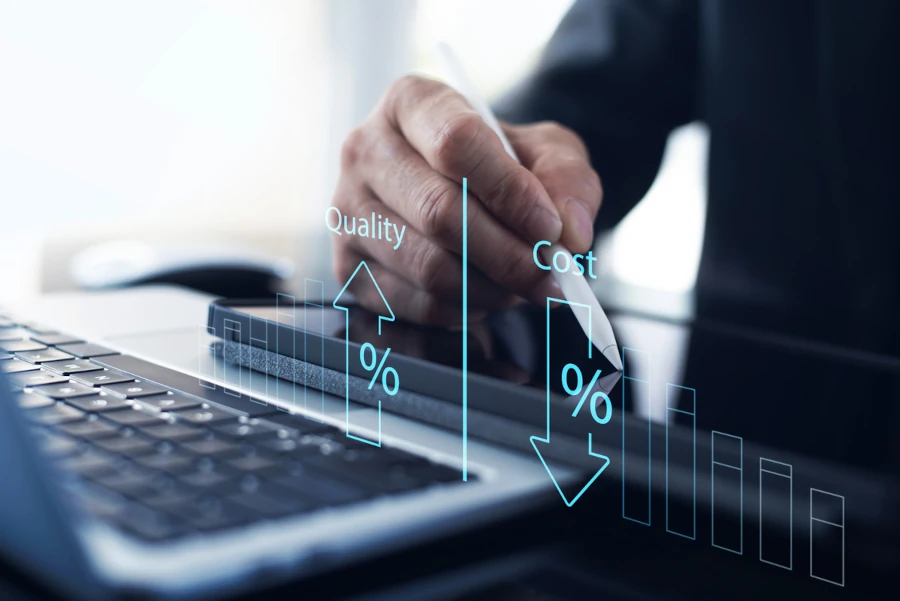
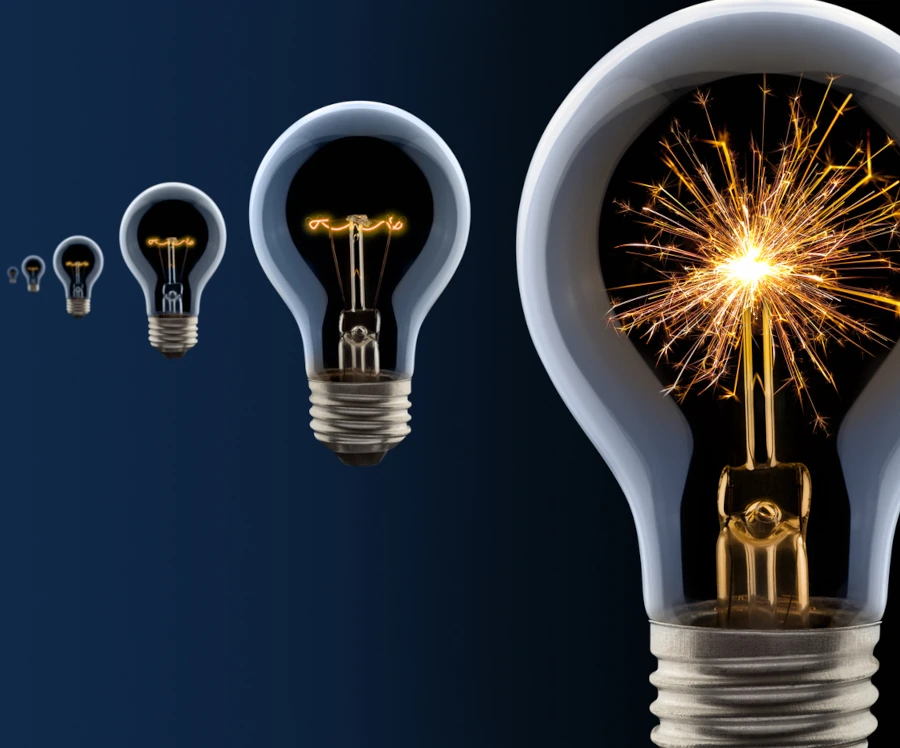
Product Enhancements
Another major advantage of additive technology is that it unlocks opportunities for product redesign that wasn’t feasible before, due to material properties or processing limitations. Consider showcasing potential new or improved features in your current parts, such as lighter-weight designs or increased functionality, as they will likely provide additional benefits, cost savings, and design flexibility.
Step Four: Contrast with the Drawbacks of Metal AM
As mentioned above, the primary benefits of metal additive manufacturing include cost savings due to the elimination of tooling, increased design flexibility, and quick turnaround times, as well as higher product quality, thanks to improved accuracy and repeatability.
To deliver a balanced assessment, when developing your business case model for MAM, you should also touch on the potential downsides of additive technologies (as illustrated in the chart below).
Metal Additive Manufacturing vs. Conventional Manufacturing
Benefits of Metal AM |
Drawbacks of Metal AM |
Reduced Overall Costs/Sustainability: less waste, no tooling, less warehousing, less working capital, less fuel consumption | Upfront Costs: Initial cost of machinery is typically more than conventional technologies (if developing an in-house facility) |
Better Design: lightweighting, hybrid materials, increased complexity, less assembly due to integrated design | Initial Learning Curve: Specialized training and knowledge of DFAM (design for additive manufacturing) are needed |
Shorter Time-to-Market: ease in design changes from prototyping to the full production of end-use parts | Post-Processing: Post-processing is usually necessary, except for end-use parts where surface finish isn’t a consideration |
Step Five: Outline Regulatory Requirements
Next, you want to understand and outline the regulatory requirements associated with additive manufacturing to ensure you're meeting all regulations -- and to avoid potential fines and penalties. When formulating your business case for additive, consider the following:
Local & International Laws
First and foremost, it’s important to understand local and international laws when working with metal AM services or equipment. These laws govern safety protocols, environmental protection measures, hazardous materials handling, data security, and other aspects of use related to additive manufacturing. It’s also critical to ensure that any personnel involved in metal AM procedures receive proper training regarding the applicable laws and regulations.
Specific Industry Standards
Most industries have their own set of rules and guidelines that must be followed, so it’s also important to consider any specific industry standards related to metal AM processes. For example, the medical sector has strict regulations concerning the production of medical devices using 3D printing technologies due to the safety issues involved with such products.
Similarly, aerospace manufacturers are subject to more stringent regulations due to their high-exposure application areas. In order to ensure that components manufactured with AM technology are up to par with existing standards, aerospace companies must adhere to strict guidelines set out by both their customer’s certification requirements and aviation regulatory bodies.
The aerospace industry is also highly regulated regarding traceability and tracking of components produced through additive manufacturing, from concept state until final installation. This requires companies to keep detailed records of entire supply chain processes as well as documented feedback loops between various stakeholders.
Intellectual Property Laws
Pay attention to any relevant intellectual property (IP) laws related to additive technologies, as well as export control regulations. These are both important factors when considering an investment in exporting printed parts across borders or collaborating on projects with foreign entities.
Bending the Limits of Metal Manufacturing with Additive
Metal AM is an excellent choice for manufacturers looking to improve part quality and functionality while simultaneously reducing costs.
Looking to reduce costs even more while still reaping all of the benefits of metal AM? Consider partnering with a manufacturer with well-established additive manufacturing technologies already in place.
Doing so alleviates the learning curve that comes with using AM, as you don’t need to train specialized staff to run the equipment. Additionally, most metal AM companies have engineers on staff that are trained in proper DFAM (design for additive manufacturing) that can assist in optimizing digital design files to be used with additive technology.
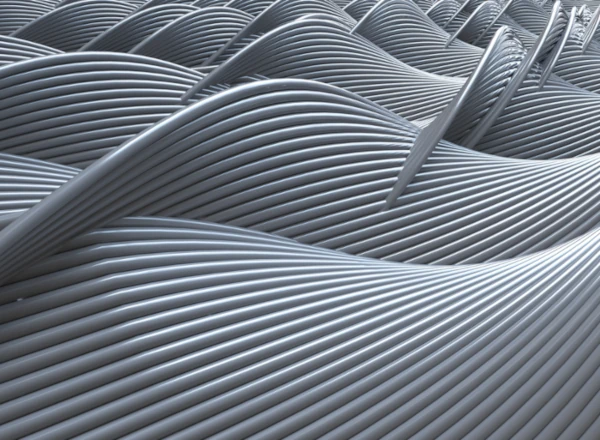