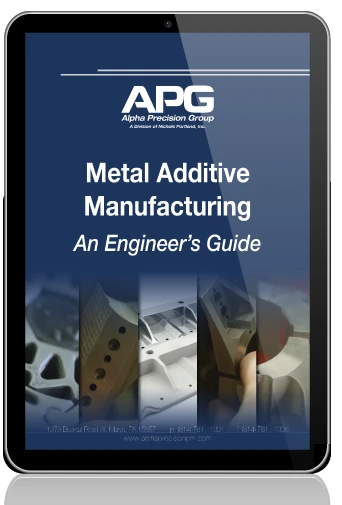
.png?width=345&height=50&name=Untitled%20(11%20%C3%97%208.5%20in).png)
Use this FREE eBook to learn more about metal additive manufacturing and what it can do for your production.
Are you tired of the limitations of traditional manufacturing methods? Does the idea of creating custom, intricate metal parts sound appealing to you?
In addition to providing unprecedented freedom of design, did you know that metal AM also reduces waste, shortens time to market, and facilitates complex assemblies & lightweighting?
Discover this and more inside this valuable resource!
Download Your Free Guide Here
What is Metal Additive Manufacturing?
Metal Additive Manufacturing (MAM) is a cutting-edge method that creates accurate, custom 3D metal parts. Using CAD models, MAM builds complex shapes, layer-by-layer, employing lasers, electron beams, and other technologies. After deposition, parts are post-processed, if a smooth surface finish is needed.
What are the Advantages and Disadvantages of Metal AM?
Metal additive manufacturing has a lot to offer your production, including:
- The consolidation of assemblies into a single part
- Ability to improve existing part properties
- Creating lightweight parts and assemblies
- Unrivaled parts customization
- Rapid prototyping and iteration of parts and assemblies
- Waste reduction
- Inventory stock reduction
- Decreasing energy consumption
- Being an ideal choice for producing high or low volumes of parts
- Allowing for distributed manufacturing
In addition to the key benefits, metal AM also presents potential disadvantages, including:
- Initial start-up cost
- Post-processing requirements
- Material limitations
Finishing Options for Metal AM Parts
Depending on the end, some components may require a surface finishing procedure before they can fulfill their final purpose. Common reasons for finishing include:
- Enhancing appearance
- Improving durability
- Adjusting shape and size
- Smoothing out uneven surfaces
- Boosting electrical conductivity
It’s important to consider the surface finishing approach during the design process - evaluating the distinct characteristics of your part is critical, as the chosen finishing technique can affect attributes, such as:
- Shape, material, thickness, and weight
- Intended function
- Performance in harsh environments
How Does Metal AM Shorten Time to Market?
Metal AM offers increased flexibility of design, reduced waste, and is cost effective, but did you know it can also shorten time to market?
Here’s how:
- Product Development Acceleration: Using MAM enables a seamless transition from CAD file to functional prototype. The design can easily be manipulated as needed, without the need for costly tooling and molds.
- On-Demand Customization: With Metal AM, you can think of a design today and print it by tomorrow.
- Ability to Test Parts Before Full Production: MAM allows you to quickly print a limited amount of parts that your customers can touch, feel, and manipulate. Changes can be easily made without adding a significant amount of time to the process.
- Hybrid Additive Manufacturing: Hybrid manufacturing, meaning the use of other manufacturing methods along with Metal AM, combines the speed, efficiency, and freedom of design of Metal AM, along with the desired benefits of other traditional manufacturing methods.