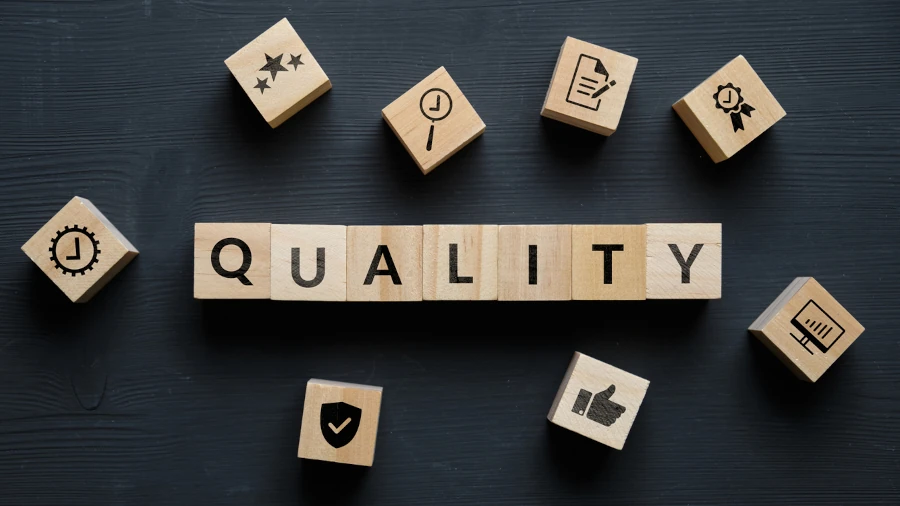
Embracing Quality Control for Additive Manufacturing
Additive manufacturing (AM), also known as 3D printing, has revolutionized the world of manufacturing, allowing for the production of complex shapes and structures that were previously impossible, or too costly, with traditional manufacturing methods.
However, amidst the excitement and innovation, a challenging question arises: How can we ensure consistent quality?
Quality control in AM isn’t as straightforward as in traditional manufacturing methods. The complexity of the AM process introduces numerous variables that can affect the final part’s quality. These variables include the quality of the raw material, the stability of the printing process, and the post-processing methods used.
Given the inherent complexities of AM processes, maintaining consistent quality and meeting industry standards can be a daunting task. This is where Quality Control (QC) steps in.
Understanding and tackling QC challenges in AM doesn’t have to feel like scaling a mountain. Here, we demystify the QC process, why it’s vital, and how you can effectively implement QC techniques in your AM processes.
What is Quality Control?
Quality control is the process of inspecting products at various stages of production to ensure they meet predetermined quality standards. It involves a series of tests and inspections to detect and correct potential defects before the final product reaches the customer. Essentially, QC acts as a gatekeeper, preventing faulty products from slipping through the cracks.
Importance of Quality Control in Additive Manufacturing
Quality control is not just a secondary process of additive manufacturing - it’s a cornerstone of the process. The significance of QC in AM extends beyond mere compliance with industry standards. Here’s a closer look at why QC is crucial:
1. Minimize Defects
In additive manufacturing, the process involves building objects layer by layer. This unique approach, while offering numerous advantages, also introduces the potential for defects that could compromise the final product’s integrity. These defects could range from structural inconsistencies, such as porosity and uneven layering, to deviations in dimensional accuracy.
Quality control mechanisms are crucial to identifying and rectifying these issues early in the process. By doing so, you can ensure your final product aligns with the intended design and meets the required standards of quality. This not only enhances the product’s performance but also boosts customer satisfaction and trust in the product.
2. Enhance Reliability
Reliability is a key factor in any manufacturing process. In additive manufacturing, the reliability of the final product is directly tied to the consistency of the manufacturing process. Quality control measures help monitor this consistency, ensuring every manufactured part meets the same high standards.
This is particularly important in industries such as aerospace, automotive, and medical, where the reliability of components can directly impact safety. By implementing stringent quality control measures, you can ensure the reliability of your products, thereby enhancing reputation and customer trust.
3. Reduce Costs
Implementing quality control in the additive manufacturing process can also lead to significant cost savings. By identifying defects or issues early on in the process, you can avoid the costs associated with rework or replacement of faulty parts.
Moreover, quality control can help optimize the manufacturing process, reducing waste and improving efficiency. This can lead to substantial savings in material costs and production time.
Regulatory Considerations: Meeting Quality Standards in Additive Manufacturing
In the high-stakes world of additive manufacturing, quality control isn’t just about creating a product that looks good and works well. It’s also about meeting the rigorous standards set by regulatory bodies, especially in industries like aerospace and medical devices.
Imagine you’re crafting a titanium hip implant or a component for a spacecraft. These aren’t just everyday items; they’re pieces that could significantly impact a person’s health or a mission’s success. That’s why regulatory bodies have set strict rules for these products, ensuring they meet the highest standards of safety, performance, and reliability.
Quality Control in AM with ISO & ASTM
The International Organization for Standardization (ISO) and the American Society for Testing and Materials (ASTM) are two of the world’s leading standards development organizations. They play a crucial role in establishing quality control standards across a wide range of industries, including additive manufacturing.
In regards to AM, ISO and ASTM standards cover aspects such as the properties of the raw materials used, the performance characteristics of the final product, procedures for testing and inspection, and the requirements for documentation and traceability. By adhering to these standards, manufacturers can ensure the quality and reliability of their additive manufacturing processes and products.
Here, we outline several current standards that pertain to additive manufacturing:
- ISO/ASTM 52901 - Additive Manufacturing - General Principles - Requirements for Purchased AM Parts: Offers detailed specifications around what customers should look for and ask for when purchasing an AM part.
- ISO/ASTM 52910 - Guidelines for Design for AM: A general guide providing requirements and recommendations for using AM in product design.
- ISO/ASTM 52900:2021 - Additive Manufacturing - General Principles - Terminology: Establishes and defines terms used in additive manufacturing technology.
As AM technologies are still relatively new, standards are still in development and are updated frequently.
Common Quality Control Techniques for Additive Manufacturing
Commonly used quality control techniques used in additive manufacturing include:
- Non-Destructive Testing (NDT)
- Statistical Process Control (SPC)
- Material Selection & Testing
- Design Considerations
- In-Process Monitoring
- Post-Processing & Finishing
1. Non-Destructive Testing
Non-destructive testing is a crucial aspect of quality control in additive manufacturing. It allows for the inspection of final parts without causing any damage, making it possible to detect internal defects that may not be visible on the surface. Techniques such as X-ray imaging, ultrasonic testing, and thermographic inspection are often used.
For example, X-ray imaging can reveal internal structures and any inconsistencies within them. Ultrasonic testing uses high-frequency sound waves to detect internal flaws or characterize materials. Thermographic inspection uses infrared imaging and thermal cameras to identify changes in surface temperature, which can indicate defects beneath the surface.
2. Statistical Process Control (SPC)
Statistical process control is a method of quality control that uses statistical methods to monitor and control the manufacturing process. It involves collecting data from various stages of the manufacturing process and analyzing it to identify any deviations from the expected output.
In additive manufacturing, SPC can be particularly useful in monitoring parameters such as the temperature and speed of the printing process, the dimensions of the printed parts, and the properties of the raw material. By identifying trends and potential issues, you can make informed decisions and adjustments to improve the quality of the final product.
3. Material Selection & Testing
The quality of the raw material used in additive manufacturing can significantly impact the final product’s quality. Therefore, it’s crucial to select high-quality materials and test them rigorously before use.
Testing involves checking for properties such as purity, particle size, and moisture content. For instance, impurities in the material can lead to defects in the final product, while the particle size can affect the material’s flowability during the manufacturing process. Moisture content is another critical factor, especially for materials like polymers, as it can affect the material’s melting and crystallization behavior.
4. Design Considerations
The design of the product can significantly impact its manufacturability and quality in additive manufacturing. Factors such as the orientation of the part, support structures, and layer thickness need to be carefully considered during the design stage.
For example, the orientation of the part can affect the amount of support needed during manufacturing, which can in turn impact the surface quality and dimensional accuracy of the final part. The design of support structures is also crucial, as inadequate support can lead to the deformation or collapse of the part during the manufacturing process. Layer thickness is another important factor, as it can affect the resolution of the final product and the manufacturing time.
5. In-Process Monitoring
In-process monitoring involves tracking the manufacturing process in real-time to detect any anomalies. This can be done using sensors that measure parameters such as temperature, pressure, and speed.
For instance, a sudden change in temperature could indicate a problem with the machine or the material, allowing for immediate corrective action. In-process monitoring can also involve visual inspection, using cameras to monitor the layer-by-layer construction of the part and identify any visible defects.
6. Post-Processing & Finishing
Post-processing and finishing are crucial stages in additive manufacturing, as they can significantly affect the final part’s quality. These steps can include cleaning, heat treatment, and surface finishing.
Cleaning involves removing any residual material from the manufacturing process, which can affect the part’s appearance and performance. Heat treatment can help relieve stresses built up in the part, improving mechanical properties. Surface finishing techniques, such as sanding or polishing, can enhance the part’s appearance and dimensional accuracy.
However, these post-processing steps also introduce the potential for defects. For example, improper heat treatment can lead to warping or cracking, while aggressive surface finishing can remove too much material, affecting the part’s dimensional accuracy. Therefore, it’s crucial to have quality control measures in place during post-processing to ensure that these steps enhance the part’s quality rather than detract from it.
Mastering the Art of Precision: Quality Control in Additive Manufacturing
In the intricate dance of additive manufacturing, quality control isn’t just a step in the process - it’s the rhythm that guides every move. As additive manufacturing continues to evolve, spreading its transformative influence across industries, quality control stands tall as the lighthouse guiding us through uncharted waters.
It’s important to commit to quality, not as a destination, but as a journey - a journey marked by precision, innovation, and a relentless pursuit of excellence.
Interested in learning more about how Metal AM can accelerate your manufacturing processes? Click below to chat with an expert today: