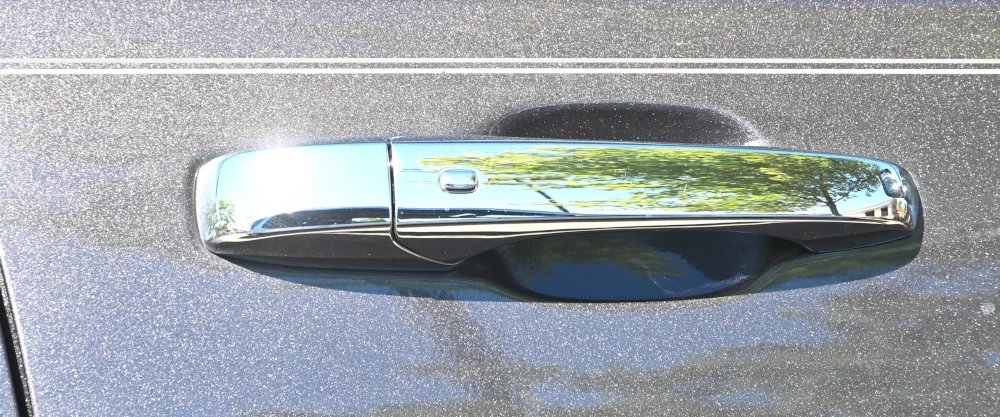
Finishing Options for Metal Additive Manufacturing
Metal additive manufacturing is a rapidly growing technology that allows manufacturers to produce geometrically complex components with great performance and durability.
Depending on their end use, some metal additive parts need to undergo a surface finishing process before they’re ready to meet those demands. Typical reasons for finishing parts can include:
- Enhancing appearance
- Improving durability by increasing resistance to wear, heat, corrosion, etc.
- Adjusting shape and size
- Smoothing out uneven surfaces
- Boosting electrical conductivity
While it may be tempting to choose your metal additive manufacturing process first and leave the post-processing as an afterthought, you should consider your surface finishing technique during the design process. It’s important to examine the unique features of your part, because the finishing option you choose can impact these features, including:
- Shape, material, thickness, and weight
- Intended function
- Performance in harsh environments
10 Surface Finishing Techniques of Metal Additive Manufacturing
Now that you know some of the reasons for finishing metal additive parts, here are some common surface finishing techniques that may boost your part’s performance:
1. Media Blasting
Here, compressed air is used to propel a blast media, such as sand, stainless steel shot, or glass beads, against the part to reduce surface roughness. This process is useful in removing surface imperfections.
2. Shot Peening
Shot peening is similar to media blasting, but with a different goal in mind. Instead of removing imperfections from the surface of your object, this process is used to increase its strength and durability.
During shot peening, pressurized air shoots metal or plastic beads at a surface, causing changes in the mechanical properties of the surface (i.e. resistance to wear).
3. Green Sanding
Green sanding is useful for reducing the appearance of printed layer lines and other imperfections. Green parts are relatively soft before sintering, so you can smooth out imperfections with a scouring pad or sandpaper before sintering.
4. Tumble Finishing
During tumble finishing, your parts are placed in a barrel along with water, an abrasive media, and a compounding agent. The rotation of the barrel causes everything to tumble down upon itself, causing friction and abrading the parts.
This process works well with large or small parts, though it’s best-suited for parts with simple geometries. Tumble finishing parts with complex geometries can lead to non-uniform finishes.
5. Vibratory Finishing
Similar to tumble finishing, vibratory finishing is another solution for finishing a large amount of parts at the same time.
During this process, your parts, media, and compounds are placed into a vibratory tub or bowl. The vibratory action causes media and parts to grind against one another, deburring and/or polishing them.
The process can be wet or dry, and very gentle or aggressive, depending on your desired surface qualities.
6. Abrasive Flow Machining
Abrasive flow machining is a type of internal surface finishing where a viscous, abrasive material is forced through the part, smoothing burrs, polishing surfaces, and removing metal. The type of additive manufacturing finishing uses a hydraulic ram to drive media through your part, creating a “slug” of abrasive material that molds itself to the part.
7. Electrochemical Polishing
An alternative to abrasive polishing, electrochemical polishing uses a chemical etchant stimulated by electrical current to smooth and treat the internal and external surfaces of a part. This process is inexpensive, though the etchant and waste products have to be handled and disposed of properly.
8. Wire Brushing
Wire brushing involves using a handheld brush, drill, or grinder for deburring, edge blending, and removing surface imperfections.
9. Heat Treatments
Similar to shot peening, heat treatments strengthen your parts by reducing tensile pressure. Heat treatments can also be used to increase density or help form parts into your final, desired shape.
10. Traditional Machining
Metal additive manufacturing post processing can include traditional methods associated with subtractive manufacturing, such as milling and grinding. These operations come into play when your manufacturer needs to further remove material to meet tolerance and surface specs.
Is Additive Manufacturing Parts Finishing Efficient?
In addition to creating highly complex parts that would be difficult or impossible to create using traditional manufacturing, metal AM allows for a wide variety of finishing options.
Virtually any finishing and post-processing method available for traditional manufacturing can translate to metal additive manufacturing. There’s an endless array of possibilities for the final look, feel, and performance of your 3D printed parts.