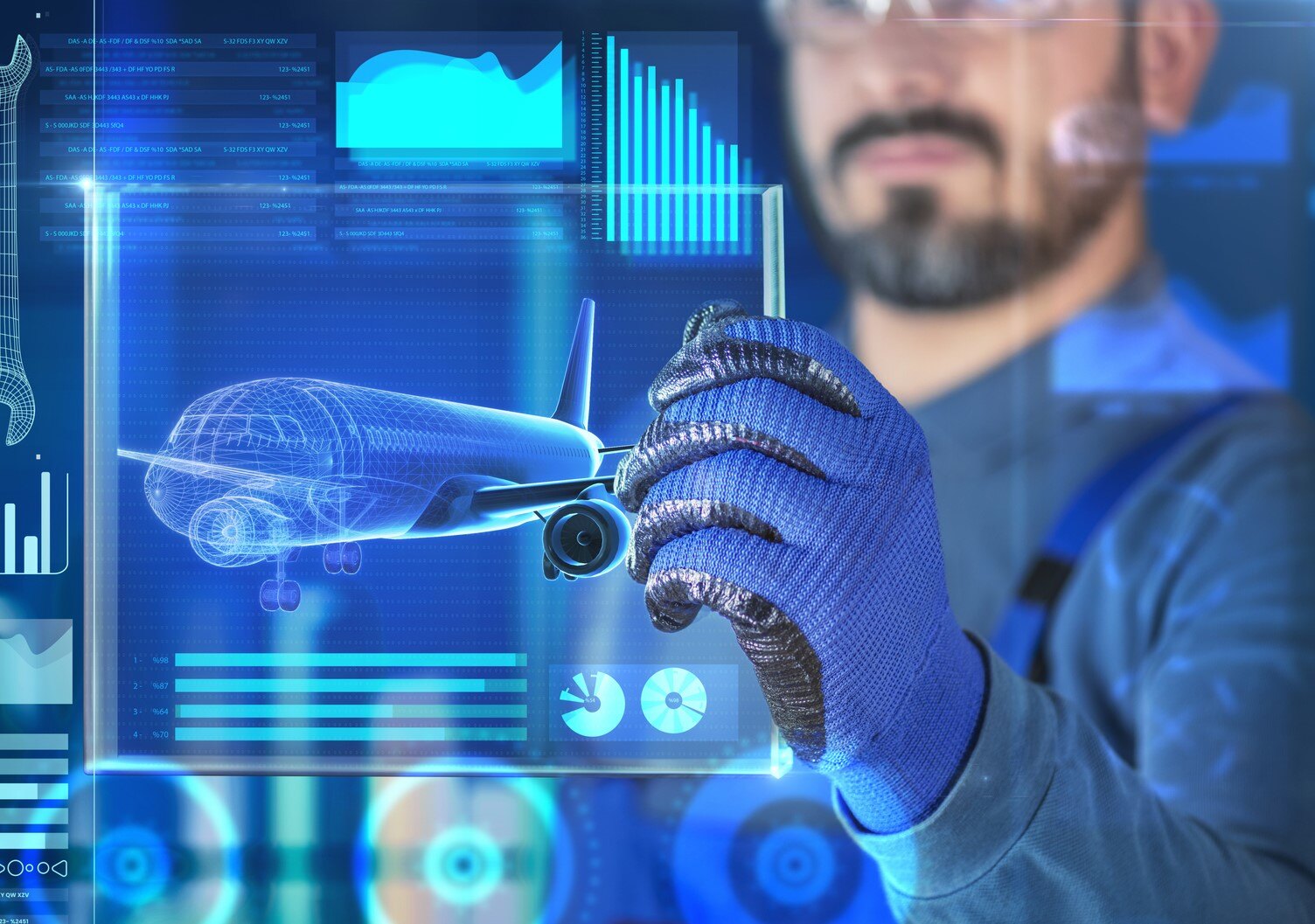
Metal Injection Molding in Aviation and Aerospace Manufacturing
When it comes to aviation and aerospace innovation, the sky is truly the limit. From fuel-efficient engines to advanced navigation systems, every component plays a critical role in helping aircraft soar to new heights. Behind the scenes of this high-tech industry, precision manufacturing methods are pushing the boundaries of what’s possible, with Metal Injection Molding (MIM) leading the way.
Aircraft and spacecraft are designed to maximize fuel efficiency and performance, thus the need for strong and lightweight components is critical. MIM not only meets this demand but also enables you to create intricate geometries and corrosion-resistant parts that are essential for thriving in the harshest environments.
Here, we’ll explore how MIM is shaping the future of aviation and aerospace component manufacturing, highlighting key benefits like lightweighting, complex geometries, and corrosion resistance.
Whether you’re part of general aviation manufacturing or involved in cutting-edge aerospace projects, understanding the power of MIM could help your designs take flight – literally.
The Role of Metal Injection Molding in Aviation and Aerospace
You’re probably asking, what makes metal injection molding so revolutionary? We’re glad you asked.
At its core, MIM combines the versatility of plastic injection molding with the strength of powdered metallurgy, allowing for the production of high-performance metal parts with exceptional accuracy. This is particularly important in aviation and aerospace, where components need to meet tight tolerances, intricate design specifications, and of course, the demand for lightweight materials.
From small, intricate parts used in cockpit systems to critical components in engines and landing gear, MIM allows engineers to bring their most complex designs to life. Metal injection molding isn’t just about manufacturing components – it’s about pushing the limits of what’s possible in design and engineering. |
Benefits of MIM For Aviation & Aerospace Manufacturing
Let’s dive deeper into the core benefits of using MIM for aviation and aerospace manufacturing:
- Lightweight Manufacturing for Fuel Efficiency
- Complex Geometries for Performance Optimization
- Corrosion Resistance & Durability in Harsh Environments
- Cost Effective Manufacturing for High Precision
1. Lightweight Manufacturing for Fuel Efficiency
One of the most significant advantages of MIM is its role in lightweight manufacturing – a crucial factor for enhancing fuel efficiency and overall aircraft performance. Here’s why weight matters so much in aviation:
- Fuel Efficiency: Reducing weight directly impacts fuel consumption. Lighter aircraft require less fuel to operate, leading to lower operational costs and a reduced environmental footprint.
- Payload Capacity: Lighter components allow aircraft to carry more cargo or passengers, maximizing the value of each flight.
Metal injection molding creates lightweight components without sacrificing strength or durability. By using materials like titanium, MIM delivers parts that are both strong and light, making it ideal for high-performance areas such as engines, structural supports, and avionics. Additionally, incorporating lightweight materials into these components not only saves fuel but also extends the flight range.
2. Complex Geometries for Performance Optimization
To achieve the peak performance aviation and aerospace demands, components often include intricate designs that traditional manufacturing methods struggle to produce cost-effectively. This is where metal injection molding shines, creating complex geometries, and optimizing part functionality and overall system performance.
These complex geometries are essential in areas such as:
- Engines: MIM creates small, detailed parts that fit into tight spaces, contributing to the overall efficiency of an engine. Whether it’s fuel injectors, turbine components, or other key engine parts, the ability to produce complex shapes without sacrificing strength is critical.
- Landing Gear: The intricate designs needed to distribute loads and absorb impact during landing are made easier with MIM. The precision of these parts ensures durability and safety in the toughest conditions.
- Cockpit Systems: Components with avionics systems often need to be compact and precisely engineered to seamlessly fit together. MIM offers the flexibility to create these detailed parts with accuracy.
By enabling the creation of complex lightweight components, MIM contributes to better aerodynamics, reduced drag, and improved fuel efficiency. Additionally, these intricate parts are manufactured with tight tolerances, ensuring reliability and longevity in harsh environments.
3. Corrosion Resistance and Durability in Harsh Environments
Aviation and aerospace components are exposed to some of the most extreme conditions imaginable – from high altitudes and temperature fluctuations to moisture and corrosive chemicals. This makes corrosion resistance a top priority when manufacturing parts for aircraft and spacecraft. Fortunately, metal injection molding excels in producing parts that are not only lightweight and strong but also highly resistant to corrosion.
Corrosion-resistant materials, such as stainless steel, high-temperature specialty alloys, and titanium alloys, are frequently used in the MIM process, offering long-lasting protection against the harsh environmental factors found in aviation and aerospace, including:
- Extreme Temperatures: Components in engines or external structures must endure intense heat or cold without degrading. MIM parts made from corrosion-resistant metals maintain their integrity, ensuring reliable performance at any altitude.
- Moisture and Salt Exposure: Aircraft flying at high altitudes or over oceans are vulnerable to moisture and salt, which accelerate corrosion. MIM components are designed to resist these elements, prolonging the lifespan of critical parts.
- Chemical Exposure: In aviation, some components come into contact with fuel, hydraulic fluids, or other chemicals. MIM enables the use of materials that withstand chemical exposure without corroding or breaking down.
These corrosion-resistant and lightweight parts make them ideal for use in critical areas such as the fuselage, engine components, and hydraulic systems. The combination of strength and corrosion resistance ensures MIM parts last longer and require less maintenance – key advantages in an industry where downtime is costly.
4. Cost-Effective Manufacturing for High Precision
Every aviation and aerospace component must meet exact specifications to ensure safety, performance, and reliability, however, achieving such a high level of precision can come with a hefty price tag. Luckily, MIM offers a cost-effective solution without compromising accuracy or quality.
MIM produces high-precision parts in large quantities at a fraction of the cost of other methods like CNC machining. Here’s how MIM delivers both precision and affordability:
- Reduced Waste: Unlike traditional machining, where significant material is removed (and often wasted) during the production process, MIM uses near-net-shape technology, meaning parts are molded to be almost the exact size and shape needed, drastically reducing material waste and cost.
- Economies of Scale: MIM is well-suited for high-volume production runs. Once the mold is created, the cost per part drops significantly, making it an ideal choice for mass production.
- Minimal Post-Processing: With MIM, parts come out of the mold with tight tolerance and smooth finishes, reducing the need for extensive post-processing, like grinding or polishing. This not only saves time but also lowers labor costs.
By offering a balance between cost-efficiency and precision, MIM meets the rigorous demands of the aerospace industry while staying within budget, making it an invaluable tool for modern aviation projects.
Soaring to New Heights with Metal Injection Molding
As aerospace technology continues to advance, metal injection molding will remain a cornerstone of innovation, delivering the precision and performance needed to help aircraft and spacecraft soar. With its many benefits – lightweighting, complex geometries, corrosion resistance, and cost-effectiveness – MIM is shaping the future of aviation and aerospace component manufacturing.
Ready to elevate your manufacturing processes? Contact us today to learn how Metal Injection Molding can take your aerospace components to new heights.