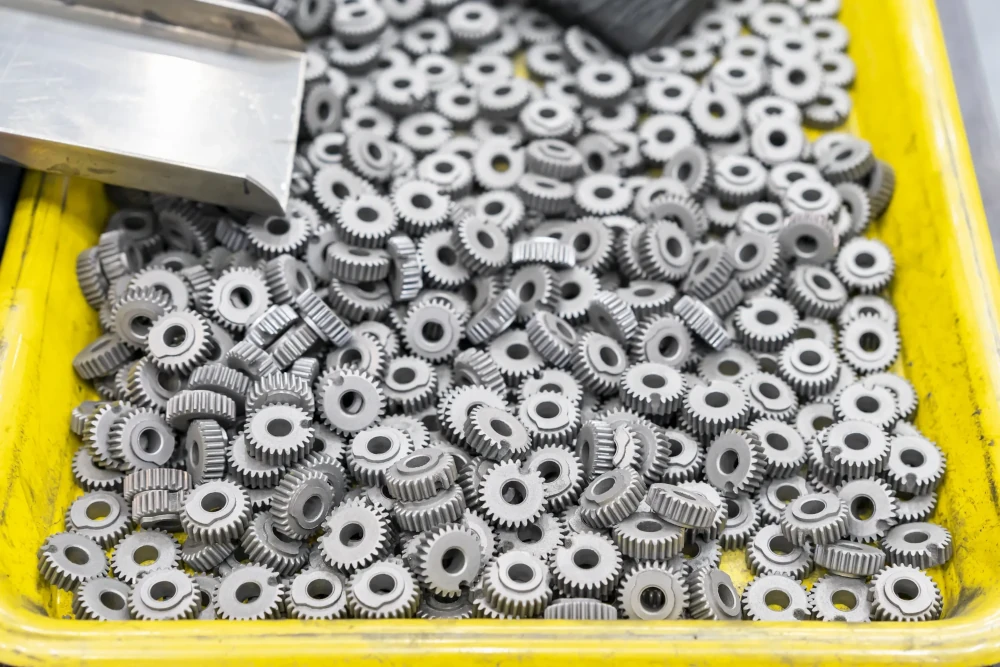
Metal Injection Molding vs. Traditional Powder Metallurgy
Metal injection molding (MIM) is a process designed to produce high-volume parts with unique, complex geometries, narrow tolerances, strong consistency, and high precision. Modeled after plastic injection molding techniques and powder metallurgy, MIM provides considerable freedom and flexibility in your choice of materials and enables a high degree of design customization.
The metal injection molding process involves precision mixtures of finely-powdered metals with polymer binder materials. The result is a feedstock that can be shaped to your specifications. It’s becoming the process of choice for a wide variety of industry applications, including agriculture, aerospace, automotive, aviation, consumer products, defense, medical, and more.
Similarities and Differences with PM
The MIM process has both similarities and differences to traditional powder metallurgy (PM). While both processes involve pulverizing metal into a powder as the base step, in traditional PM, the metal powder is irregular in shape and pieces come in larger sizes, this is due to the water atomization process. Alternatively, during the MIM process, the powder is spherical in shape due to the requirements for flowability, and this is achieved through a gas atomization process. Powder metallurgy end products achieve lower results on the theoretical density scale when compared to MIM parts.
The powder metallurgy process is very economical for very specific geometries, but it does have limitations due to the motion of the tooling. One limitation, to be specific, is no side action capability for undercut features. This would be one reason a customer may lean to MIM for a specific application. However, one downfall for the MIM process is that the material is more expensive than the PM material due to the gas atomization and the compounding of the binder and metal particles to produce MIM feedstock.
The Metal Injection Molding Process
The metal injection molding process consists of four steps: preparing the feedstock, molding, debinding, and finally, sintering. Each step will be discussed briefly below:
1. Preparing the Feedstock
The specified metals are atomized into an extremely fine powder that’s usually under 20 microns, added to a heated thermoplastic binder, thoroughly combined, and then allowed to cool. This mixture is then granulated into uniform pellets made of around 60 percent powdered metal and 40 percent polymer binder.
2. Injection Molding
The feedstock is re-melted and injected into the same type of cavity molds used in plastic injection molding. The feedstock cools and solidifies into the specified part design. At this point in the process, the part is considered “green.”
3. Debinding
Once the part has cooled and solidified, the polymer is removed by one of three options: a water process, solvent process, or catalytic process. This removes a considerable amount of the volume per piece, something that needs to be taken into consideration during the design process. At this point in the process, the part is considered “brown.”
4. Sintering
Parts are sintered in a furnace at high temperature, consolidating the empty spaces by 17-22%, depending on the alloy system. The result is a high-density part reaching 95-99% theoretical density of wrought material. The part will shrink down to between 75-85% of its pre-sintered size. Your MIM provider needs to account for the shrinkage on each geometry, specifically in the design phase. MIM parts achieve good dimensional accuracy, which typically does not require secondary operations for tolerance.
Benefits of Metal Injection Molding
Metal injection molding produces extremely complex geometries economically and with great repeatability when compared to competing technologies.
MIM also provides engineers with a higher level of customization over traditional PM due to the inherent process differences.
Pros and Cons of MIM
While MIM is a great option for many applications, traditional powder metallurgy may be the preferred choice at times.
Two of the biggest differences are cost and energy expenditure. The additional polymers and steps in the MIM process add to the expense of production, and it takes more energy to produce the pieces. Powder metallurgy is less expensive generally and takes less energy. In addition, some pieces require more porosity and a high degree of control over the microstructure for lubrication or oil retention. In such cases, traditional PM may be the optimal choice over MIM.
Another difference is the typical cost of tooling. This is due primarily to the higher level of complexity of the final part geometry. MIM tooling on average is slightly more expensive than traditional PM tooling.
Industries Using MIM
Metal injection molding is a preferred process for manufacturing a wide range of parts across many industries. Some examples include:
- Automotive—Ignition locks, actuators, fuel injectors, seating mechanisms, locking components, solenoids, etc.
- Aerospace—Fittings, latches, seating components, spray nozzles, vane adjustments levers, high-performance engine and safety components, etc.
- Medical—Endoscopy instruments, surgical instruments, implant components
- Dental—Brackets, buccal tubes, etc.
- Electrical—Connectors, switches, etc.
- Defense—triggers, sights, safeties, blocks, and more.
Which Process Will You Choose?
As you can see, both MIM and traditional PM have positives and negatives. Ultimately, the right process for your component will depend on a variety of factors, including the amount of design freedom you need and the end use of the component being manufactured. Fortunately APG is capable of many unique metal forming processes, two of which being MIM and traditional PM.
To keep up with the latest MIM resources, visit our blog.