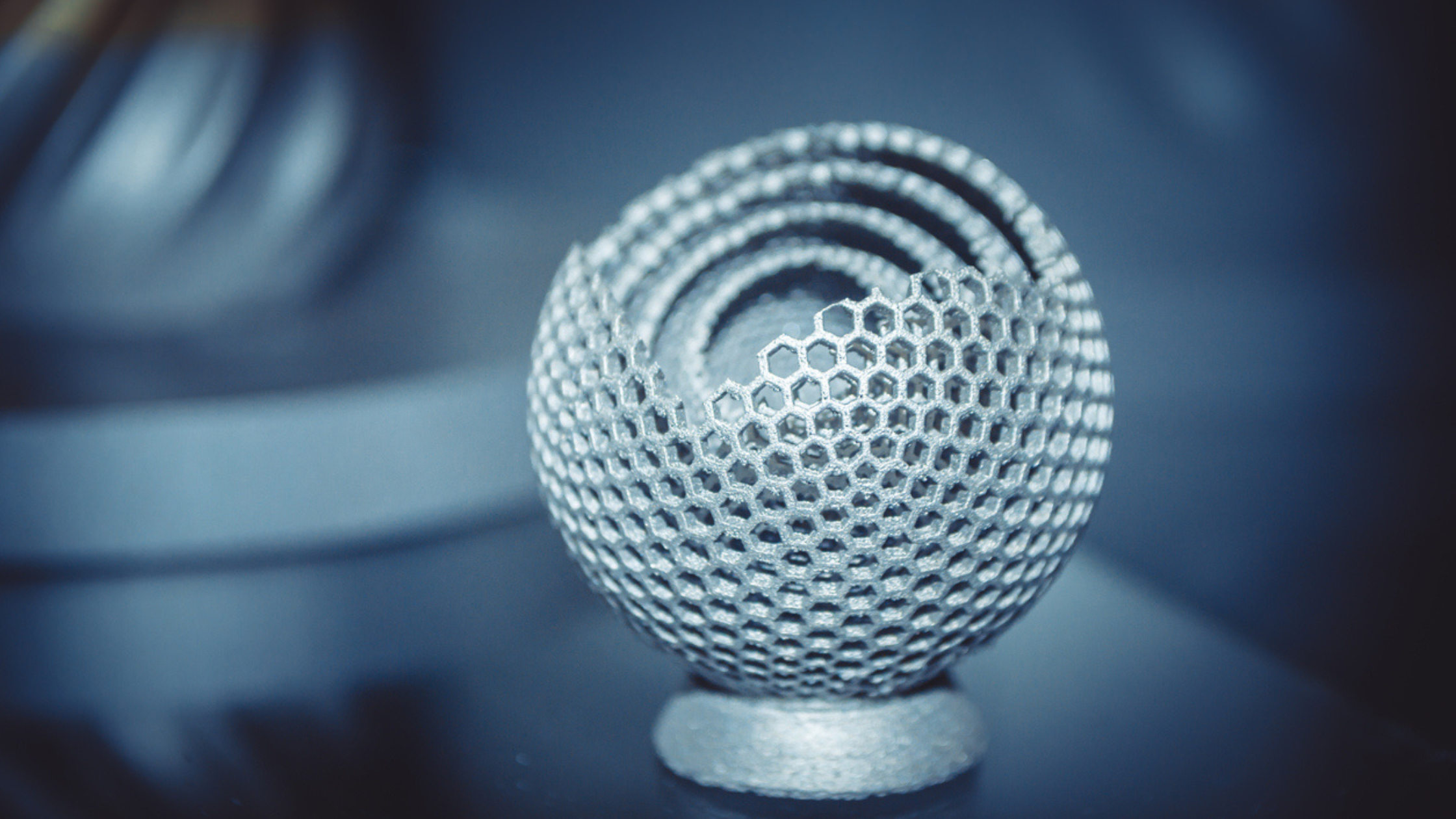
The Effects of 3D Printing Layer Thickness in Additive Manufacturing Processes
Metal additive manufacturing (also known as metal AM) is a type of industrial 3D printing that produces three-dimensional parts, layer by layer, from powdered metal.
Each of these 3D printed layers have a specified thickness, which is a measure of the layer height of each consecutive addition of material in the additive manufacturing process.
In this post, we will talk about layer thickness, its effect on speed and cost of 3D printed components, and when to use a thicker versus thinner layer.
What is Layer Thickness in 3D Printing?
To understand layer thickness better, let’s look at Selective Laser Sintering (SLS), which is a type of metal additive manufacturing process that uses powder bed fusion to build 3D parts.
During the SLS process, powdered metal material is transferred from containers onto the build stage with a recoating tool. A laser then selectively scans the thin layer of metal powder, sintering the particles together. The build platform descends one layer and the recoating tool transfers more powder to the surface of the first layer. The laser scanning process repeats, adhering it to the previous layer, making a solid part, layer by layer.
It’s important to note that not all 3D printers are created equal. Technical differences between the different additive manufacturing technologies generate different layer thicknesses, with some generating a lower layer height than others. To adjust layer height, you can change the settings of the printer before printing your 3D file.
Here’s a chart of the different 3d printing minimum and maximum layer thicknesses of different materials for reference.
Effects of 3D Printing Layer Thickness on Speed and Cost of Components
The number of layers required to create a 3D component determines the printing speed and printing time required. The lower the layer thickness, the longer it will take to print your object.
For example, an object that’s 1cm high may require 100 layers at 100 micrometers or 167 layers at 60 micrometers. Despite using the same additive manufacturing technology, the cost of printing goes up when using thinner layers.
How to Choose a Layer Height
Before choosing a 3d printing layer height, think about your desired component and consider these qualities:
- Geometry
- Application
- Post-Processing
1. Geometry: Does the Component Have Curves and Angles?
The effect of layer thickness in 3D printing is seen more on curves and angles and is less visible on straight vertical walls, due to the layer-by-layer nature of the process.
For example, if your model has a print hole along a horizontal axis, the 3D slicing program has to separate the hole into multiple layers and stack them on top of one another, creating an uneven edge that resembles a staircase. This “stepping effect” becomes more prominent on surfaces with greater curvature.
If your design has a significant number of curves or holes, using a lower layer height will result in a more accurate part.
2. Application: What Will the Component Be Used For?
Layer height has an impact on the vertical resolution of your component, which in turn affects its smoothness. If your main concern is visual appearance, selecting a lower layer height is the way to go for a smoother finish.
When functionality or economics are your main concerns, using a higher layer height is ideal, which will reduce print time having a positive effect on total cost.
3. Overall Cost: Will the Component Go Through Post-Processing?
When choosing a layer height, it’s important to think about whether the printed components will go through post-processing. For example, if a part is going to go through a polishing or mass finishing operation, an evaluation would be necessary to compare reduced layer thickness cost impact vs. additional polish processing to account for larger layer thickness.
Conclusion
The layer height you choose depends on the final geometry, appearance, functionality, and post-processing techniques (or lack thereof) used during the metal additive manufacturing process.
The two main takeaways of choosing layer height include:
- You should use a lower layer height for parts with curved surfaces or if visual appearance is important.
- Using a higher layer height is faster and more cost-effective.
Interested in learning more about metal AM? Check out the resources in our blog.