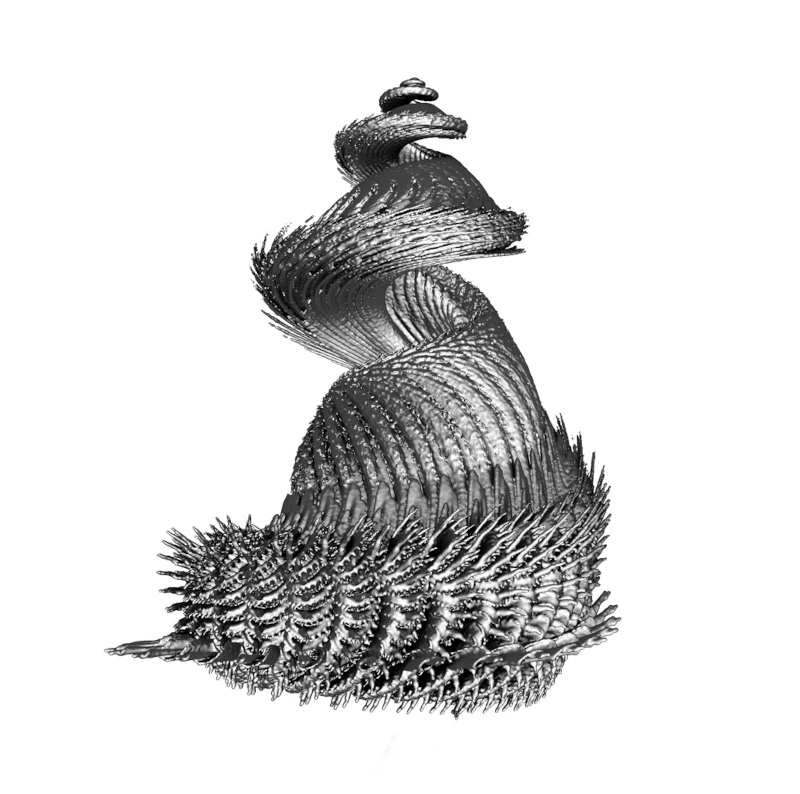
Guide to the Metal Additive Manufacturing Process From Start to Finish
The global additive manufacturing (AM) industry market was valued at $13.84 billion in 2021 and is projected to grow at a compound annual growth rate (CAGR) of 20.8% by 2030.
Despite the benefits metal AM offers - freedom of design, ability to consolidate assemblies into a single part, lightweighting capability - some industries have been slow to adopt the technology, partly due to misconceptions about the additive manufacturing process.
To help you better understand the applications, pros, and cons of additive manufacturing, we compiled an explanation of how additive manufacturing works, from start to finish.
What is Metal Additive Manufacturing?
Metal additive manufacturing (also known as metal AM) is a type of industrial 3D printing that produces three-dimensional parts, layer-by-layer, from powdered metal. The difference between 3D printing of the past and today’s additive manufacturing is that the latter goes beyond prototyping -- the process results in strong, 3D parts for a wide variety of industries and applications.
Materials used can vary from metal to biochemicals, thermoplastics, and ceramics, depending on which additive manufacturing process is being used.
Examples of additive manufacturing technology include:
- Directed energy deposition
- Binder jetting
- Material extrusion
- Material jetting
- Sheet lamination
Six Steps of the Metal Additive Manufacturing Process
The six steps of the metal additive manufacturing process consist of:
- Design 3D Model Using Computer Aided Design (CAD)
- STL File Creation and File Manipulation
- Machine Setup
- Building Layer by Layer
- Part Removal
- Post-Processing
1. Design 3D Model Using Computer-Aided Design (CAD)
The first step in the additive manufacturing process is designing a digital 3D model of your part. The most common way to achieve this is through CAD software, though some metal additive manufacturing companies use reverse engineering to create models via 3D object scanners.
Regardless of which tools you use, you’re creating a replica of the 3D model, so it’s crucial to make sure every detail is precise and modeled to the right shape and size.
2. STL File Creation and File Manipulation
Next, the CAD file is converted into another format, such as standard tessellation language (STL) or an additive manufacturing file (AMF).
These file formats capture all surfaces of the model by stitching triangles of various sizes on its surface. The main difference between the two is that AMF can support color, materials, lattices, and castellations while STL solely supports the surface geometry of the object.
The file is then imported into a slicer program that converts it to G-code.
- G-code tells the printer what to do and how to do it, allowing you to customize the parameters of your object, including layer height, support, and part orientation.
3. Machine Setup
The setup process for additive manufacturing varies depending on which technology you use. Variables include:
- Model orientation
- Material selection
- Printer temperature
- Support structure, build platform leveling, and more.
During this step, print material, binders, and other consumables are loaded into the machine. The raw materials require careful handling and often have a limited shelf life.
Note: Additive manufacturing machines consist of many small and intricate parts, so operators must maintain and calibrate them regularly to produce accurate prints.
4. Building Layer by Layer
The printer gradually builds the model by depositing one layer at a time. This process can take hours or days to complete, depending on the:
- Printing machine
- Build size
- Additive manufacturing technology
- Printing resolution.
Most metal AM machines don’t need oversight after the print starts. If a problem does arise, it’s usually because the machine ran out of materials or there was a software error.
5. Part Removal
Sometimes removing a print is as simple as separating the printed part from the build platform and support structure.
However, some industrial 3D printing methods require a technical process that involves extraction of the print while it’s still attached to the build plate or encased in build material. In situations like this, a highly skilled machine operator with proper safety equipment is a must.
6. Post-Processing
Post-processing varies depending on the printer technology and materials used.
For example:
- Metal parts may need to be stress-relieved in an oven.
- Parts produced with stereolithography (SLA) technology must be cured under UV light before handling.
- Prints created through fused deposition modeling (FDM) can be handled immediately.
- Support structures may need to be removed.
Post-processing techniques include:
- Sanding
- Tumbling
- High-pressure air cleaning
- Polishing
- Coloring
When is Metal Additive Manufacturing Right For the Job?
So when is additive manufacturing the right process for the job? Consider the following design considerations.
- Are you prototyping/testing out new designs?
- Is your design geometrically complex?
- Are you looking to combine more than one component into one assembly?
- Do you want to lightweight your part?
- Are you looking to personalize or customize your parts?
- Are you looking to streamline a bridge-to-production process?
- Are you less concerned with surface finish?
- Is this a niche product with a lower volume?
If you answered yes to any of these questions, MAM may be a great choice for your production process.
Working With a Metal Additive Manufacturer
If you’ve decided metal AM can improve your part’s performance or cost efficiency, the next step is to find a metal additive manufacturer that can meet your needs. If you’re unfamiliar with the capabilities of the metal additive manufacturing process, look for a supplier that:
- Has experience specific to your industry
- Offers in-house design & engineering guidance
- Has the appropriate certifications & standards, and understands how to help you meet yours.
With a baseline understanding of how metal AM works -- plus the guidance of an experienced supplier -- your component can exceed what you thought possible with AM.
Ready to learn more? Check out our other blogs.
Editor’s Note: This blog was originally published on 10/1/21 and was updated on 12/7/2022.