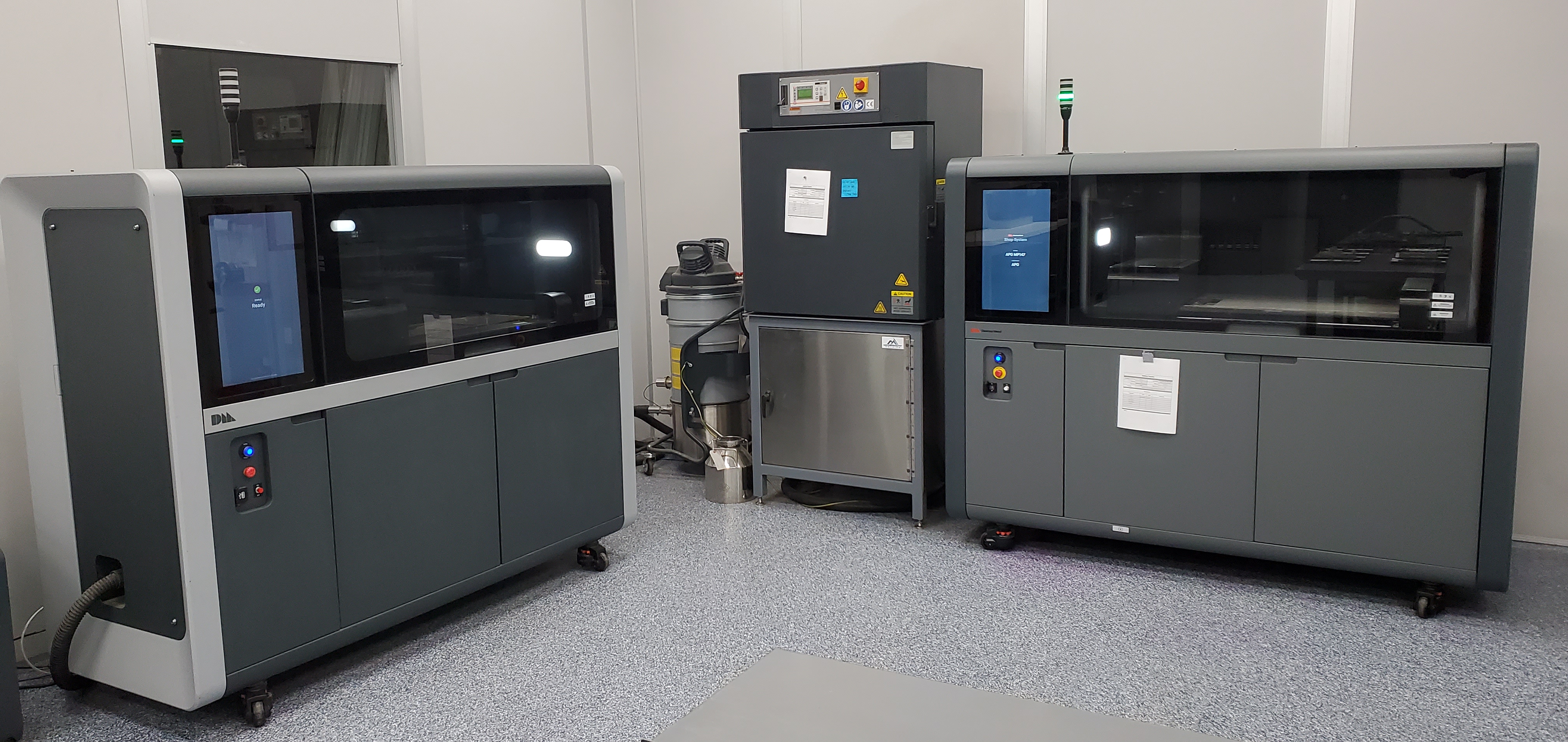
Additive 101: The Metal Binder Jetting Process Explained
The engineering and design world is starting to learn that additive manufacturing can answer their prayers for merging speed and precision in a single project. What’s more of a mystery is this: What’s the best way to additively manufacture a piece of metal?
Advantages of Binder Jetting Technology
Among the many, many methods of manufacturing metal, Binder jetting is one of the fastest and most accurate forms.
There are many advantages (and even a few disadvantages) to the binder jetting process. We’ve compiled a list of both to help you decide whether this type of metal AM is the best way to meet your performance, lead time, and cost requirements.
What is the Metal Binder Jetting Process
The process is referred to as a type of additive manufacturing because it adds material during the process, as opposed to subtractive manufacturing techniques (milling, grinding, cutting, etc.) that remove material from a solid block. Layers are added, rather than taken away and scrapped, leading to less waste.
During the binder jetting process, a binding agent is selectively deposited onto a powder bed, bonding the areas together to form a solid part, one layer at a time. Similar to traditional paper printing, the binder functions like the ink as it moves across the layers of powder, which, like paper, transform into the final product.
Advantages of Metal Binder Jetting
Binder jetting has the edge in several cost and quality factors, compared to not just other metal AM processes, but also many non-AM processes:
- You can produce multiple iterations of a single part in one print, reducing part costs and development time
- Printing supports are not always necessary, cutting down on wasted material and post-processing time
- Binder jet systems can recycle and reuse up to 99% of stray powder
- Manufactured parts are isotropic, meaning they’re equally strong in all directions
- Rapidly advancing technology is enabling the production of larger parts and opening paths to a wider range of material options
- Ability to produce complex designs without increasing costs
Disadvantages of Metal Binder Jetting
There’s no perfect metal manufacturing process -- otherwise, why would they all exist? Drawbacks of binder jetting include:
- Higher equipment costs compared to subtractive manufacturing techniques
- Today, post-print processes are largely manual, but significant development to automate the steps is underway
- Requires additional equipment for post-processing
When to Use Metal Binder Jetting
Metal binder jetting is used in a variety of markets, including:
- Industrial applications
- Aerospace components
- Dental and medical devices
- Part casting
Common applications for binder jetting include:
- Rapid tooling, fixtures, and jigs
- Rapid to fully functional prototypes
- The dense and durable metals used in binder jet printing make it a prime choice for end-use products as well
Design Roadblocks?
Metal binder jetting is quickly becoming a popular technology for manufacturers who want an efficient, cost-effective way to produce custom parts out of a wide variety of metals. Like any metal manufacturing process, it has its quirks, but an experienced vendor can help steer you around any design roadblocks.
To learn more about whether metal binder jetting can support your product development, contact us.