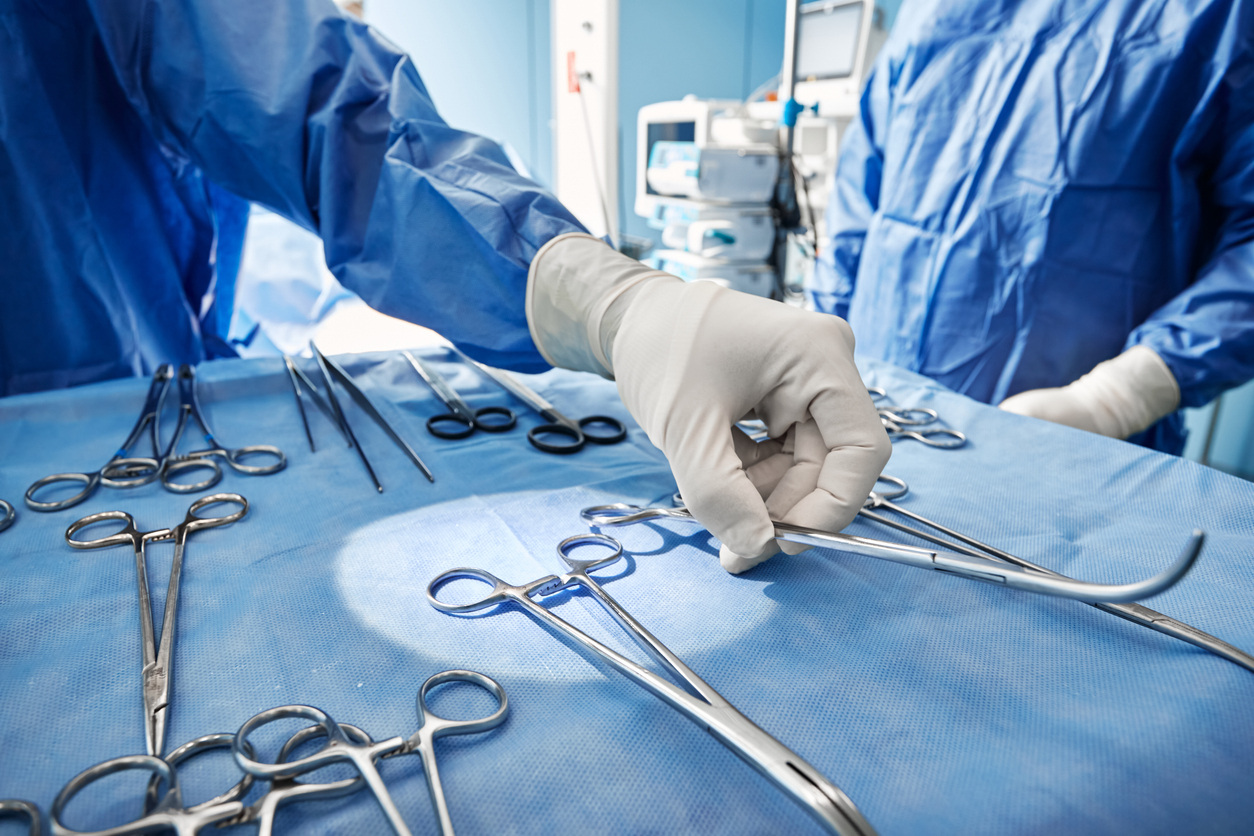
The Benefits of MIM for Surgical Instrument Manufacturers
Metal Injection Molding (MIM) is making significant strides in the medical industry, particularly in manufacturing surgical instruments—the ability to create small, intricate parts with exceptional precision fuels this advancement. MIM is particularly beneficial for crafting surgical tools with complex designs that are too complicated for traditional machining.
This innovative process is a game-changer, enabling rapid prototyping and mass production of highly detailed components critical in modern surgeries. In this article, we will explore how MIM's benefits can advance surgical instrument manufacturing, helping manufacturers stay ahead of the industry curve.
The MIM Advantages for Superior Manufactured Surgical Instruments
Metal Injection Molding (MIM) produces small, complex parts by combining the benefits of powder metallurgy and injection molding. The process begins with metal powders mixed with a binder to create a feedstock that can be injected into molds. The precision comes from the tight tolerances possible with this method, allowing manufacturers to develop components that are not only small in size but also feature complex geometries that would be challenging or impossible to achieve with traditional machining techniques.
The ability to design and produce parts with intricate shapes means that surgical instruments can have features like fine contours, precise fittings, and detailed surface textures, which are necessary for their functionality. Moreover, MIM's capability to produce these detailed components in a single step reduces the need for multiple manufacturing processes, which can introduce errors and increase production time. MIM stands out as a key technology in the medical field, facilitating the production of advanced surgical instruments that meet the highest standards for precision and reliability.
There are 4 key benefits of MIM for surgical instrument manufacturers:
- Range of biocompatible metals
- Customization of material selections
- Cost efficiency
- Minimized waste during production
Range of Biocompatible Metals
MIM can manufacture surgical instruments using various biocompatible metals, including:
- Stainless steel
- Titanium
- Cobalt Chrome
Because of their strength, resistance to corrosion, and compatibility with bodily tissues, these materials are widely used in the medical business.
Stainless Steel
Stainless steel is favored for its excellent corrosion resistance and strength, making it ideal for surgical instruments that require durability and hygiene. This material's strength ensures the longevity and reliability of surgical tools, even through strenuous sterilization processes. Stainless steel's adaptability improves the functionality and performance of surgical instruments. It opens up new opportunities for innovation and design, allowing manufacturers to tailor products to specific surgical needs and improve patient outcomes.
Titanium
On the other hand, titanium is favored for its lightweight nature and exceptional biocompatibility, making it ideal for surgical implants and instruments that require minimal reactivity when in contact with biological systems. This material versatility enhances the performance and longevity of surgical instruments. It opens up new opportunities for innovation and design, allowing manufacturers to tailor products to specific surgical needs and improve patient outcomes.
Cobalt Chrome
Cobalt chrome alloys are widely used in surgical tool manufacture due to their outstanding strength and wear resistance, which provides longevity even after repeated usage. Cobalt chrome is known for its exceptional biocompatibility, corrosion resistance, and ability to tolerate extreme sterilizing treatments necessary in medical environments. These qualities make cobalt chrome an excellent choice for precision surgical equipment and orthopedic implants that require dependable performance and longevity. This material's durability also promotes innovation in medical device design, allowing for the development of more effective and patient-specific surgical treatments.
Customization of Material Properties
MIM also offers the ability to customize the material properties of surgical instruments to meet specific medical requirements. By adjusting the composition of the metal powders during the feedstock preparation, manufacturers can fine-tune properties such as strength, flexibility, and hardness. This means that instruments can be engineered for particular tasks—whether that involves creating a flexible tool that can endure repetitive motion or a rigid instrument designed to take on high stress during surgical procedures.
Cost Efficiency
Cost efficiency is a significant advantage of MIM for surgical instrument manufacturers operating in a competitive market. The MIM process allows high-volume manufacturing to reduce production costs significantly compared to traditional machining methods. By consolidating multiple manufacturing steps into a single process, MIM minimizes waste and optimizes material usage, lowering expenses.
The reduced need for manual labor and shorter production times mean manufacturers can scale their output without an affiliated cost increase. This efficiency improves profitability and allows manufacturers to offer competitive pricing while maintaining quality standards.
Minimized Waste During Production
One of MIM's standout features is its capacity to reduce material waste during manufacturing. Unlike traditional machining methods, which often involve cutting away excess material from a larger block, MIM uses a feedstock that is shaped and injected into molds. This near-net-shape approach provides only the necessary material to create each component, leading to minimal scrap.
Most excess powder from the MIM process can be recycled and reused, reducing overall waste. By optimizing material usage and incorporating recycling practices, MIM contributes to cost savings for manufacturers and promotes a more sustainable manufacturing environment. This aligns with the growing demand for eco-friendly practices in the medical industry. This commitment to waste reduction can improve a manufacturer's reputation and competitiveness while supporting broader environmental goals.
The Specifics in Biocompatibility for Manufacturing MIM Parts
The biocompatibility of MIM parts is an essential connection in the production of surgical instruments, as it directly impacts patient safety and the effectiveness of medical devices. MIM employs materials such as stainless steel and titanium, which are well-established for their biocompatibility. These materials do not react negatively when in contact with biological tissues, making them ideal for surgical applications. MIM's controlled manufacturing process reduces contaminants, resulting in parts that abide by stringent medical standards. Using manufactured surgical instruments produced by MIM promotes patient safety and improves the reliability of instruments used in major surgical procedures.
Superior Material Properties
MIM technology creates parts with superior material properties that are widely used in surgical applications, such as:
- 304L stainless steel
- 316L stainless steel
- 17-4 PH stainless steel
- Titanium alloys
The process creates a uniform microstructure, yielding reliable mechanical performance and durability. This uniform distribution of metal particles enhances the strength and toughness of the instruments, allowing them to withstand the stresses encountered during surgical procedures. Additionally, the isotropic properties achieved through MIM ensure that the material behaves consistently in all directions, reducing the risk of failure. These superior characteristics make MIM parts a preferred choice for manufacturers seeking to produce high-performance surgical instruments that can meet the evolving needs of the medical field.
One of the main factors that make MIM achieve high density and low porosity in the final parts after the sintering process. Sintering is when the injected components are heated to a temperature that allows the metal particles to bond without reaching their melting point, resulting in a solid product. High density has a compact structure that improves the surgical instruments' mechanical strength, ensuring they can withstand the demands of medical procedures.
Additionally, low porosity reduces the presence of any faults within the material, which can be critical in medical applications as they can lead to not meeting medical standards and increased risk of contamination. Maintaining a low porosity level, MIM-manufactured parts exhibit extremely tough and durable characteristics needed for manufactured surgical instruments that face repeated use and sterilization cycles. This contributes to maintaining patient safety and improving surgical outcomes, reinforcing the importance of MIM in the medical device industry.
MIM-produced surgical instruments can be designed and manufactured following FDA and ISO standards, which involve thorough testing for biocompatibility, mechanical performance, and sterilization examinations. The MIM process already uses top-quality biocompatible materials, helping manufacturers meet necessary regulations smoothly.
Adhering to quality management systems, such as ISO 13485, ensures manufacturers maintain consistent quality throughout production. By focusing on compliance with medical standards, MIM enhances the marketability of surgical instruments and helps build trust with healthcare providers and patients, ultimately leading to better patient outcomes.
Want to learn more about Quality Control in Medical Device Manufacturing?
Read on here
Outsourcing Production to a MIM Partner
Partnering with a specialized MIM manufacturer like APG offers surgical instrument manufacturers the following:
- Strategic advantage in the industry
- Providing expert knowledge
- Cutting-edge production techniques
- Adaptability to the competitive market
This collaboration improves manufacturing capabilities and considerably reduces the time-to-market for new surgical tools, allowing companies to respond swiftly to evolving healthcare demands and regulatory requirements.
Ready to Upscale Your Surgical Instrument Manufacturing?
Contact us today to discover how our MIM solutions can help you achieve excellence and innovation in every tool you create. Explore the possibilities of reducing production time, increasing consistent product precision, and meeting stringent industry standards while remaining cost-effective.
Let us help you navigate the complexities of modern surgical instrument manufacturing with our tailored MIM strategies.