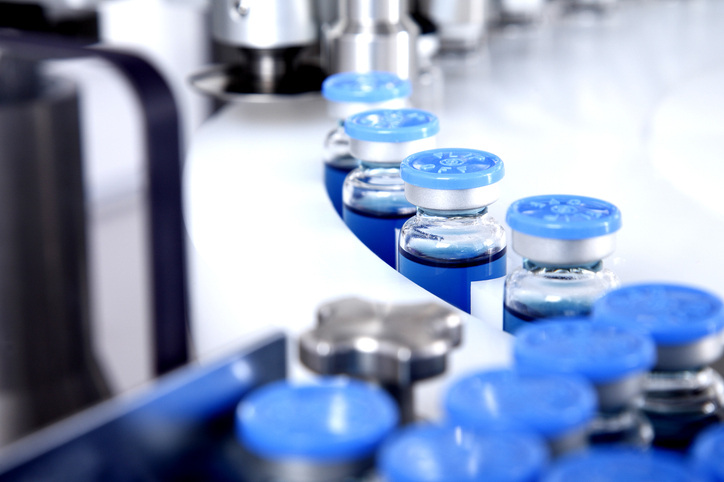
Quality Control in Medical Device Manufacturing with Metal Additive Manufacturing
What provides the reliability and safety of your medical devices while leveraging the latest in manufacturing technology?
Quality control in additive manufacturing.
Metal additive manufacturing (MAM) is a game-changer in the medical device industry, offering exceptional accuracy and customization. However, assuring consistency and reliability in production remains a challenge.
Why is quality control so important?
Without rigorous quality control, the benefits of MAM could be compromised, leading to defects in final products. This is important for the medical field, where the stakes are high and the margin for error is low.
The solution? Advanced quality control methods that raise the bar.
Integrating statistical process control (SPC) and failure mode effects analysis (FMEA) with Six Sigma frameworks guarantee the highest standards of product safety and performance
The result? Medical devices you can trust are backed by the most stringent quality control measures available.
Faster, Smarter Production: Quality Control in Additive Manufacturing for Medical Devices
Additive manufacturing has been a key factor in maintaining consistent quality control in medical device production. This breakthrough technique allows the development of customized medical devices, greatly improving both productivity and quality control. Using CAD software, manufacturers can produce tailored devices that meet specific patient needs, reducing the risk of errors and improving patient outcomes.
The changes brought on by additive manufacturing go beyond customization; they have also increased production speed and efficiency. Traditional manufacturing methods are often time-consuming and resource-oriented. However, additive manufacturing allows rapid prototyping and reduces material waste, resulting in shorter lead times and lower costs. The ability to quickly run continuous designs and produce small batches efficiently allows medical device producers to better adapt to market needs and regulatory changes. As a result, the combination of improved quality, faster production times, and increased adaptability positions additive manufacturing as a key force in the future of medical device production.
Transforming Medical Device Production with Metal Additive Manufacturing
Metal additive manufacturing (MAM) in the medical industry has opened up new avenues for designing and producing custom-made medical devices.
One main application this has increased is in creating orthopedic implants, where MAM allows the development of highly complex structures customized to the patient’s unique anatomy. This customization improves fit, biocompatibility, and better overall outcomes for patients undergoing joint replacements or other orthopedic procedures.
Additionally, metal additive manufacturing is making significant strides in dentistry, especially in producing complex dental restorations. With MAM, dental professionals can create custom-fit crowns, bridges, and implants that match the patient’s dental architecture and improve durability and aesthetic appeal. These innovations highlight the transformative potential of metal additive manufacturing in the medical industry, where customized solutions can considerably improve patient care and streamline manufacturing processes.
Production Powerhouse: Technologies in Medical Manufacturing with MAM
The manufacturing process can be improved with innovative technological features such as custom solutions and productivity improvements. These features include:
Binder Jet technology: This innovative approach in additive manufacturing uses a liquid binder to bond powder materials layer by layer. This process has gained traction in medical manufacturing due to its ability to produce complex geometries with high accuracy and a range of material options, including:
- Metals
- Ceramics
- Composites
One of its main advantages is the notable reduction in post-processing requirements, allowing for a faster time to market. However, while Binder Jet technology facilitates customization, challenges such as binder burnout and additional strength treatments must be managed to guarantee durability and performance in medical applications.
Moldjet from Tritone: This technology developed by Tritone focuses on a unique method of depositing material into printed wax molds, which can be very beneficial in creating complex shapes and structures tailored for specific medical devices. Moldjet is highly used because it can combine high-quality surface finishes directly into the manufacturing process, reducing the need for manual finishing work.
These two technologies provide medical device manufacturers with flexibility. Like Binder Jet technology, Moldjet faces challenges such as the up-front equipment investment and the complexities of designing build files that meet the product specifications. This technology is a long-term investment that minimizes waste and presents an attractive alternative in the medical device production industry.
The progress in Binder Jet and Moldjet technologies brings significant advantages to medical manufacturing. These new techniques improve manufacturing productivity by allowing for faster and more exact fabrication of complex medical components. There are many ways in which the two featured technological applications help, including:
- Reduced Time to Market: Accelerates the production process, allowing for quicker access to new products.
- Enhanced Product Customization: Facilitates the creation of tailored solutions, such as orthopedic implants that match individual patient anatomy.
- Efficient Small Batch Production: This method supports the manufacture of small quantities without compromising quality, making it ideal for specialized medical needs.
- Improved Surgical Outcomes: Custom fittings can improve results and increase patient satisfaction post-surgery recovery.
- Agility in Regulatory Compliance: Allows manufacturers to swiftly adapt to changing regulations and market demands, maintaining a competitive advantage.
Want to learn more about the impact MAM has on the medical industry?
Read more here
Strength Meets Safety: Alloys Transforming Implants
To be sure of optimal performance and safety, these alloys are carefully engineered to meet several requirements of the medical industry, including:
- Biocompatibility
- Mechanical strength
- Corrosion resistance
Innovations in alloy formulations, such as titanium-based or cobalt-chromium alloys, demonstrate superior biocompatibility and mechanical properties, making them ideal for implants and devices that interact directly with biological tissues.
These materials are thoroughly biocompatible and mechanically strong, tested to ensure they are fit for medical equipment. Biocompatibility assessments examine how materials interact with bodily tissues, ensuring they do not trigger any adverse reactions. At the same time, mechanical strength tests evaluate stiffness, fatigue resistance, and toughness to guarantee that devices can withstand them in everyday situations. Adopting new alloys significantly affects device functioning as they help to create lighter, stronger, and more durable devices to improve both performance and patient safety.
Navigating FDA Regulations for Quality Control in Additive Manufacturing
The regulations for additive manufacturing in the medical device sector are governed by the FDA's framework, which sets standards to guarantee the safety and effectiveness of innovative technologies. The FDA evaluates additive manufacturing processes through premarket submissions, focusing on specific features of AM products such as materials, design, and consistency. This regulatory control is necessary as AM might produce customized medical devices that would not be covered by traditional regulatory procedures. Companies should be ready to show how their production process considers the subtle details of additive technology while complying with standard safety procedures.
The FDA's Additive Manufacturing Program plays a major role in advancing regulatory science, facilitating an exchange between innovators and regulators. This project promotes integrating best practices in design and quality reliability and is meant to help develop and validate AM processes and materials. Engaging with industry stakeholders helps the program create rules that could promote compliance and innovation simultaneously.
For manufacturers adopting additive technologies, it’s important to partner with an organization that is certified and educated on FDA controls. A knowledgeable partner provides valuable insight on how to follow regulatory requirements, to make sure products are compliant and market-ready. This partnership not only decreases risks associated with regulatory delays or non-compliance but also improves the credibility of the products being developed. By leveraging the expertise of certified professionals, manufacturers can confirm that their additive manufacturing processes align with FDA standards, eventually leading to safer and more effective medical devices for patients.
Achieving Quality Control in Medical Device Manufacturing
Combining quality control methods between metal additive manufacturing and traditional manufacturing processes is necessary for consistency and reliability in medical device production. Approaches like statistical process control (SPC) and failure mode effects analysis (FMEA) can be applied to monitor and improve the quality of metal AM processes. These techniques allow manufacturers to identify potential variations and defects early on in production, quickly adjusting for product safety and efficacy.
Advanced methodologies such as the Six Sigma framework are also key in driving continuous improvement initiatives within the manufacturing environment. This approach focuses on reducing variability and minimizing flaws by applying statistical analyses. Six Sigma may be used in additive manufacturing to:
- Accelerate processes
- Maximize material use
- Support regulatory standard compliance
By leveraging these modern quality control methods, manufacturers can improve the integrity of their products and ensure they meet the high expectations of healthcare professionals and patients.
Unlock the Future of Medical Device Manufacturing with Alpha Precision Group
Additive manufacturing transforms medical device manufacturing by providing customization, speed, and reliability. This cutting-edge technology allows the development of extremely complicated, patient-specific devices, which leads to better patient outcomes and lower production costs.
Ready to Step Up Medical Device Manufacturing with APG?
As the medical device business evolves with advances such as metal additive manufacturing, the demand for precision and quality has never been greater. Alpha Precision Group is at the cutting edge of technological innovation, offering additive manufacturing solutions suited to your specifications.