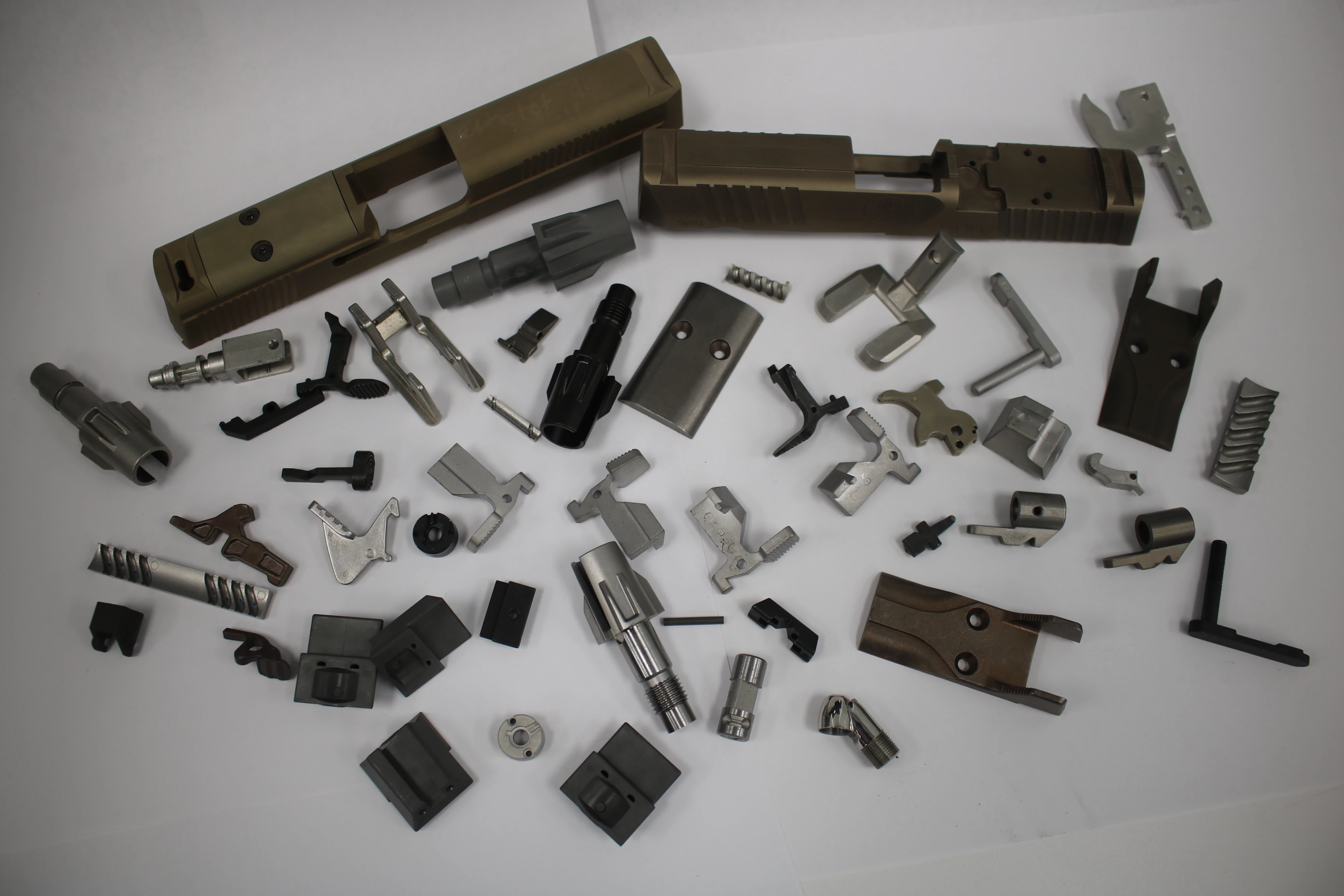
Technical Considerations to Look Out for in Medical Additive Manufacturing
Imagine you have a hip replacement that doesn’t allow you to sit down comfortably. Or, a knee replacement that doesn’t let you bend your leg.
Without the proper manufacturing method, that would be the case of implants or replacements. Fortunately, medical additive manufacturing (AM) exists and offers flexibility and biocompatibility with medical devices.
5 Technical Considerations in Medical Additive Manufacturing
It’s no secret that medical additive manufacturing has to be accurate in every application. To ensure accuracy, there are 5 technical considerations in medical additive manufacturing to look out for.
- Biocompatible metal materials
- Design for additive manufacturing (DfAM) in medical applications
- Bone scaffold 3D printing
- Surface finish and post-processing for implants
- Rapid prototyping in medical applications
1. Biocompatible Metal Materials
Selecting the proper material is essential for patient safety and implant/prosthetic longevity. Oftentimes, titanium and its alloys, stainless steel, or cobalt-chrome are used to meet these standards.
Titanium
Titanium is the most commonly used material in medical additive manufacturing. It has an excellent strength-to-weight ratio, superior corrosion resistance, and biocompatibility. Additionally, Titanium promotes osseointegration, making it an ideal material for orthopedic implants such as joint replacements.
Stainless Steel
Stainless steel is also widely used in medical additive manufacturing. This material offers strength and corrosion resistance, while still being an affordable choice. Typically, stainless steel isn’t used for implants due to its lower biocompatibility and tendency to release ions into surrounding tissues. However, it is ideal for other applications such as surgical tools.
Cobalt-Chrome Alloys
The properties of cobalt-chrome alloys surpass titanium and stainless steel. Cobalt-chrome alloys are suited for high-stress applications (such as knee or hip replacements), where wear resistance and strength must be superior. Despite their advantages, the stiffness of cobalt-chrome alloys can lead to stress shielding, where the implant takes on more stress than the surrounding bound – which can lead to failure over time.
2. Design for Additive Manufacturing (DfAM) in Medical Applications
Medical devices must offer ergonomic design, patient-specific customization, and integration of complex features. Unfortunately, traditional manufacturing doesn’t meet these design requirements – but fortunately, medical additive manufacturing does.
By using DfAM, devices can be tailored to fit the anatomical dimensions of the patient while accommodating individual biomechanical movements. This customization ensures that prosthetic limbs or orthopedic devices not only fit properly but also enhance mobility and reduce discomfort during use.
3. Bone Scaffold 3D Printing
When designing and printing bone scaffolds, pore size, structure for osseointegration, and material strength must be considered. However, it’s challenging to mimic nature's bone architecture while also ensuring biocompatibility.
Pore Size
Bone scaffold design requires careful consideration of pore size and overall porosity. It’s a fine line – the porosity of the scaffold should be high enough to promote bone tissue growth and vascularization, but also needs to maintain the mechanical strength needed to support the surrounding bone structure.
Structure for Osseointegration
Osseointegration – the direct structural and functional connection between living tissue and the surface of a load-bearing artificial implant – is vital for the success of bone scaffolds.
The overall architecture of the scaffold, including the design of the interconnecting pores, should support the formation of new bone tissue and its integration with the existing bone.
Material Strength
The material used for bone scaffolds must possess sufficient mechanical strength. Without this strength, the scaffold could degrade or collapse before the new bone tissue can take over the load-bearing function.
The choice of material depends on the specific application but typically is a biocompatible metal such as titanium or resorbable polymers.
4. Surface Finish and Post-Processing for Implants
The surface finish of medical implants plays an important role in success and longevity. This aspect of implant design and manufacturing directly influences biocompatibility, tissue integration, and the risk of postoperative infections.
Fortunately, post-processing in additive manufacturing promotes an optimal, clean surface finish that allows for integration ease and low-contamination risk with the implants.
5. Rapid Prototyping in Medical Applications
The application of metal additive manufacturing for rapid prototyping in the medical field has drastically changed how medical devices and implants are designed, tested, and refined. This technology offers unparalleled speed, cost-effectiveness, and flexibility, significantly impacting device development and patient outcomes.
Metal AM allows digital designs to be turned into physical parts in a matter of hours or days, greatly reducing the development cycle of medical devices and implants. In turn, this lowers costs by allowing one prototype to be made at a time. For custom implants or tools needed in urgent cases, the speed of metal AM can be life-saving.
Unlocking the Potential of Medical Additive Manufacturing
Now, imagine you have a hip replacement that allows full movement and flexibility. Or – a knee replacement that allows you to run the way you did before.
However, with medical additive manufacturing, these are now possibilities. With superior flexibility, strength, and biocompatibility, implants and replacements are becoming smoother transitions than ever before.
Ready to Take the Next Step?
If you’re ready to integrate medical additive manufacturing into your processes or gain access to top-tier products produced by AM, reach out to our team of experts at Alpha Precision Group today.