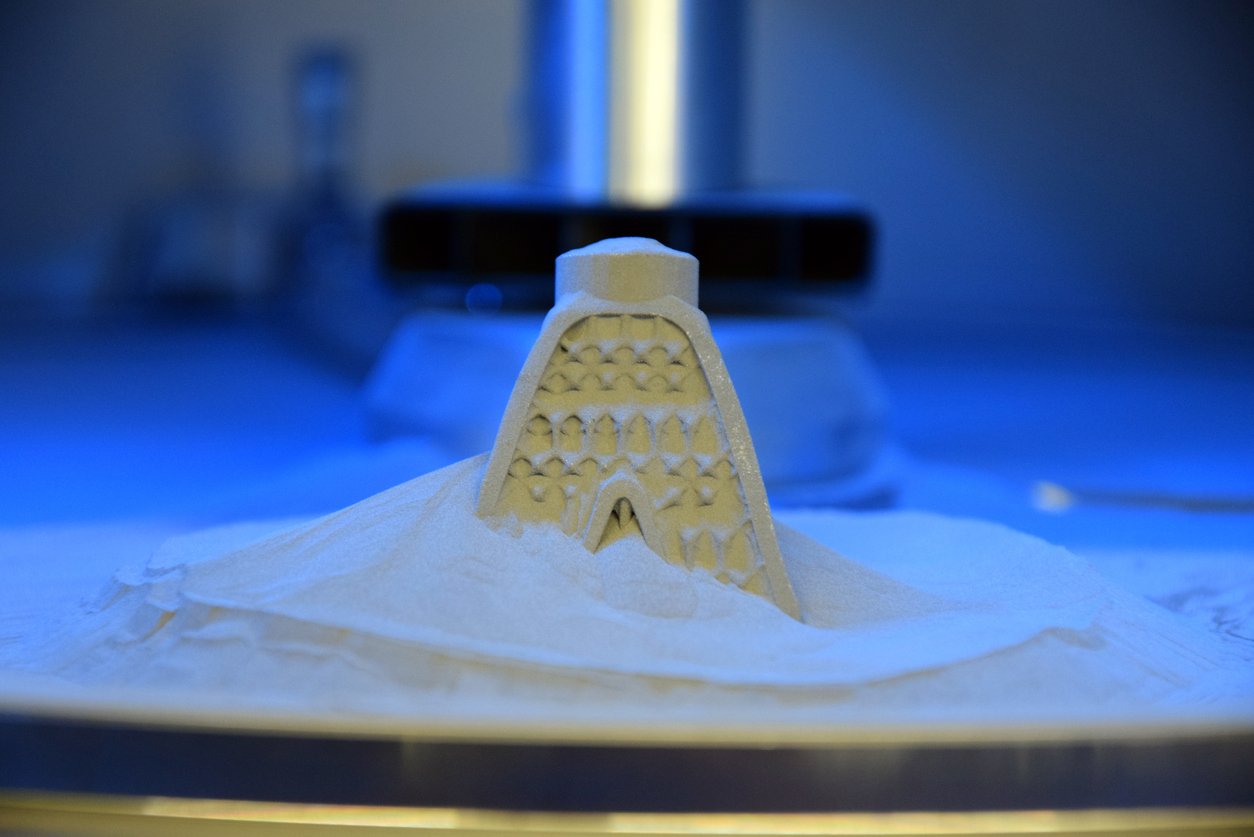
4 Common Challenges in Metal Additive Manufacturing
Metal 3D printing has evolved significantly in a seemingly short about of time. While it's come a long way from its inception in the mid-1980s, there are still a few challenges that you need to look out for.
When it comes to manufactured parts, the last thing you want is your product to be riddled with deformations, whether they’re readily visible or not. Not only is this extremely frustrating, but it can set project timelines back to a point of no return.
Unfortunately, hiccups and mistakes are a natural occurrence in every manufacturing process, and the metal additive manufacturing process is no exception.
What is Metal Additive Manufacturing?
Before we begin examining some common challenges with Metal 3D Printing, let's take a look at what Metal Additive Manufacturing is.
The Metal Additive Manufacturing process (also referred to as metal AM) uses metal powders to create strong, complex components for a variety of industries and applications. It’s best described as: "producing components through the deposition of material, layer by layer.”
Different Additive Manufacturing processes can take on materials other than just metal, such as biochemicals, thermoplastics, and ceramics.
Some Additive Manufacturing technology examples include:
- Binder Jetting
- Material Extrusion
- Material Jetting
- Sheet Lamination
- Directed Energy Deposition
4 Metal 3D Printing Issues to Avoid
The metal AM process comes with several advantages, such as the ability to produce complex shapes and be flexible with your design choices. However, there are a few specific issues to avoid, including:
- High Porosity & Low Density
- Residual Stress
- Stair-Stepping
- Lack of Quality Consistency
1. High Porosity & Low Density
The term “porosity” refers to tiny air cavities that form within a component during production. Although generally very minuscule (think microscopic), these pores can reduce the overall density of parts, thus increasing the likelihood they’ll crack or fatigue over time.
Porosity usually happens in two primary ways.
First, gas pockets sometimes form within the power feedstock during the powder atomization process. Although this issue isn’t as common, it highlights the importance of purchasing materials from a reliable supplier.
The second way that pores form is through the additive process itself. This can occur if the powder particles are bigger than the actual layer thickness of the part, or if the powder being added is loosely packed. This second way is contingent on the additive process that you've selected to go with for your parts creation.
As you've likely guessed, high porosity leads to low part density - the more tiny holes and gaps there are in a part, the lower the density will be. When a part is printed, its mechanical properties have to be gauged, as a part with sub-standard density has a higher likelihood of cracking and failing under load.
So what can you do to avoid high porosity parts?
Your manufacturing partner should make sure your design matches up appropriately with your material specification. They should also own the equipment capabilities to compact your part effectively, brushing aside any concerns about cavities or pores forming. Be sure to inquire about mechanical testing following printing and during the prototyping phase.
2. Residual Stress
Residual stress, which can crack or warp components, might be the metal additive manufacturing process’s most common issue.
This stress occurs during the heating-cooling process, which inherently causes components to expand and contract. Extreme heating and cooling have to happen frequently due to their integral nature in the additive process, regardless of which technology is being used.
Residual stress is the most troublesome at the center of parts, along with the interface between the part and the substrate to which it adheres. Support structures can be added to help reduce residual stress but can deform the part throughout the process if not used properly.
Work with someone who has previous metal AM expertise, as they will understand how to support the part’s unique shape without adding deformities.
3. Stair-Stepping
This is one of the biggest cosmetic challenges that metal additive manufacturers face.
“Stair-stepping” is the nickname given to the layering error that causes a part’s finish to look similar to a staircase. In other words, the final layer isn’t smooth and has a slight, unintended incline.
Luckily, this is a minor issue as there are many post-processing technologies that can smooth out your part's uneven surfaces, increase the overall part strength, improve surface properties, and give it the shine that you're looking for.
4. Lack of Quality Consistency
This issue exists in nearly every manufacturing process, but it’s something to avoid at all costs in large orders. And while a big step in consistent quality is selecting the right raw material, the manufacturer you choose is ultimately responsible for overall quality control.
If 1,000 of the same component are ordered, each one should be within a very tight variance of one another. Otherwise, there’s a risk of losing functionality in part of the batch.
This may be an issue common to the industry, but can be minimized simply by selecting an expert team of metal additive manufacturers.
Get the Additive Manufacturing Checklist
Wondering if Metal AM is the right process for your job? Get your free checklist today and find out.
Editor's Note: This page was originally published on Oct. 27, 2021 and was updated Sept. 27, 2022