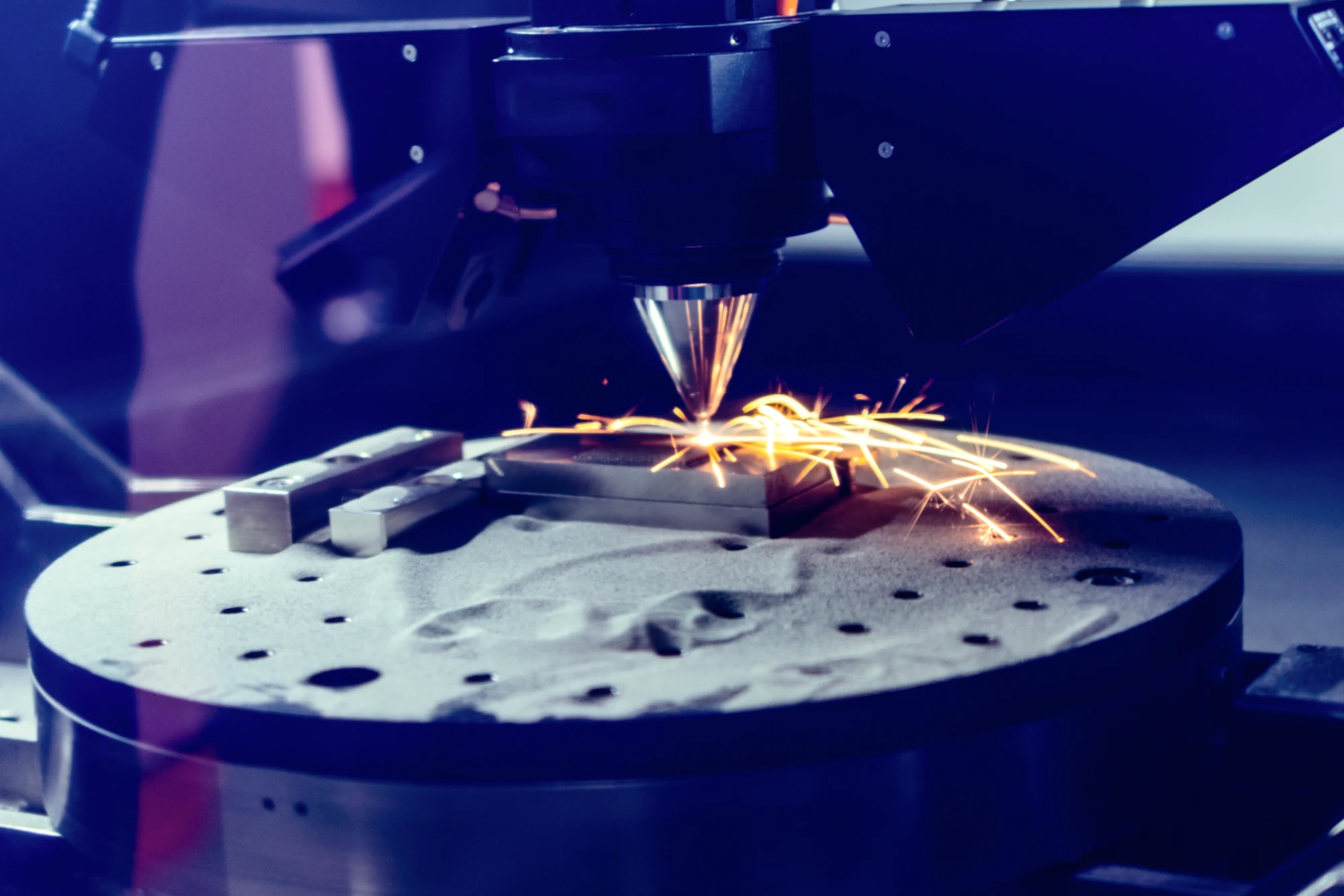
Comparing Electron Beam Melting vs. DMLS in Metal Manufacturing
Over the years, metal additive manufacturing has progressed from a novelty for rapid prototyping to a technology that can mass produce end-use products. MAM has been divided into several offshoots, including two of the most well-known processes, electron beam melting and direct metal laser sintering (DMLS).
Today we’re going to take a look at the electron beam melting and DMLS processes, including benefits and limitations, and common areas of application of each technology.
What is Electron Beam Melting?
During the electron beam melting process, an electron beam fuses metal particles to create a 3D part. This process takes place in a vacuum chamber to ensure a clean, controlled build environment and to prevent oxidation.
As with any additive manufacturing process, electron beam melting begins with a 3D model created in a computer-aided design (CAD) program. The file is sent to a slicing software that converts the model into printing instructions that are sent to the chosen machine.
How Does Electron Beam Melting Work?
- A thin layer of metal powder is deposited onto the build plate.
- As the powder is preheated, an electron beam melts the powder in the areas specified by the 3D file.
- The next layer of metal powder is deposited, and the electron beam melts and fuses the layers.
- The process repeats until the part is complete.
- Excess powder is removed, and the part undergoes post-processing, including sanding, polishing, and heating in an oven.
The Benefits of Electron Beam Melting
Electron Beam Melting (EBM) offers unique advantages in additive manufacturing that make it a standout choice for industries seeking efficiency and precision. Here’s a closer look at why EBM is increasingly favored:
Higher Power and Faster Printing
Unlike lasers, the electron beams used in EBM are more powerful, enabling them to handle complex, high-strength materials with ease. Multiple electron beams can operate simultaneously, significantly reducing printing times and boosting productivity.
High-Density Parts and Prototypes
EBM technology ensures that the powder material is entirely melted, resulting in parts and functional prototypes with high density. This complete melting process leads to parts with superior mechanical properties and durability, which is ideal for high-performance applications.
Recyclable Material
With EBM, unused powder does not go through the sintering furnace, making it recyclable and reducing material waste. This feature not only cuts costs but also supports sustainability initiatives within manufacturing workflows.
Reduced Support Requirements
EBM requires fewer supports compared to laser powder bed fusion technologies. This reduced dependency on support structures streamlines post-processing and minimizes the risk of material distortion, ultimately enhancing design flexibility and reducing production time.
Limitations of Electron Beam Melting:
While Electron Beam Melting (EBM) offers numerous advantages, it also has certain limitations that may impact its suitability for specific applications. Here are some of the primary drawbacks to consider:
Limited Material Compatibility
EBM is currently compatible with only a few metals, primarily titanium and chromium-cobalt. This limited material selection can be restrictive for industries requiring a broader range of metals in their manufacturing processes.
Reduced Precision
Compared to laser-based 3D printing technologies, EBM has reduced accuracy due to its slightly wider electron beam. This can lead to less precise parts, requiring additional post-processing to meet exact specifications.
Higher Costs
The materials and machines used in EBM are considerably more expensive than traditional manufacturing methods. High costs can be a barrier for companies looking to implement EBM, especially for smaller-scale operations or prototyping.
Small Build Volume
EBM printers currently have limited print volume, with the largest available model offering a maximum build space of 350 x 350 x 380 mm. This smaller print volume restricts the size of parts that can be created in a single print, which may not be ideal for larger applications.
Rough Surface Finish
Parts produced via EBM generally have a rougher surface finish than those created with Direct Metal Laser Sintering (DMLS). Additional finishing steps may be required, adding time and cost to the production process.
Applications of Electron Beam Melting (EBM)
Electron Beam Melting (EBM) is highly valued for its ability to produce dense, durable parts, making it a preferred technology in several specialized industries. Beyond rapid prototyping, EBM is widely used in the following fields:
Aeronautics and Motorsports
The strength and high-density capabilities of EBM-produced parts make it ideal for creating components such as fuel nozzles and engine chambers. Aerospace companies, like SpaceX, often rely on additive manufacturing techniques like Direct Metal Laser Sintering (DMLS) for similar applications, capitalizing on the robust properties that EBM can provide.
Medical Industry
EBM is instrumental in the production of custom medical implants, including prostheses and skull implants. The technology’s ability to deliver strong, biocompatible parts makes it especially suitable for personalized medical solutions that must adhere to precise specifications to ensure patient safety and comfort.
What is Direct Metal Laser Sintering (DMLS)?
During the DMLS process, a high-wattage laser slowly moves across the print surface, where it sinters metal powders and alloys. Additional layers of powder are applied and sintered until the object is complete.
3 Key Differences: Electron Beam Melting vs. DMLS
While Direct Metal Laser Sintering (DMLS) shares similarities with Electron Beam Melting (EBM) in both processing and post-processing, there are three key differences that set them apart:
1. Melting Process
In DMLS, the metal is not heated to the point of complete melting. Instead, the process sinters the powder, fusing particles at a lower temperature than in EBM, where the powder is fully melted.
2. Atmosphere Requirements
DMLS does not require a vacuum environment, unlike EBM, which must operate in a vacuum to function properly. This difference simplifies the setup for DMLS and can reduce associated costs.
3. Energy Source
DMLS uses a high-powered laser instead of an electron beam. This laser-based approach allows for a narrower, more precise energy source compared to the wider electron beam used in EBM.
Benefits of Direct Metal Laser Sintering (DMLS)
Direct Metal Laser Sintering (DMLS) offers significant advantages in metal 3D printing, making it a go-to choice for complex and high-strength applications:
Material Versatility
DMLS is compatible with a wide range of metal alloys, providing flexibility in material choice to meet specific project requirements.
Complex Geometries
The precision of DMLS enables the creation of intricate geometries that would be challenging, if not impossible, to achieve through traditional machining or casting.
High-Strength Parts
Parts produced with DMLS exhibit excellent strength and mechanical properties, making them suitable for demanding applications across various industries.
Recyclable Powder
Unused powder in the DMLS process can be collected and reused, supporting cost efficiency and sustainability in production.
Limitations of Direct Metal Laser Sintering (DMLS)
While DMLS offers unique advantages, it also has limitations that may affect its application for certain projects:
Limited Build Size
Smaller build volume compared to other additive manufacturing technologies, such as Fused Deposition Modeling (FDM), limiting maximum part size.
High Machine Costs and Moderate Accuracy
DMLS machines are significantly more expensive than binder jetting machines and are not as accurate, which can be a drawback for high-precision applications.
Porosity in Finished Parts
DMLS parts are more porous than those produced with Electron Beam Melting (EBM). While porosity can be managed during processing or post-processing, it cannot be eliminated.
Expensive Metal Powders
Metal powders for DMLS are costly, typically ranging from $300 to $600 per kilogram, which can make material costs prohibitive for large production runs.
Applications of Direct Metal Laser Sintering (DMLS)
DMLS is widely utilized across several industries, demonstrating its versatility and effectiveness for specialized applications:
Medical Industry
DMLS is used to produce custom prosthetics in high-strength materials, with controlled porosity that promotes bone integration, enhancing the stability and longevity of implants.
Dentistry
DMLS allows for the production of durable dental prosthetics, including bridges, crowns, and partial dentures, tailored to individual patients for optimal fit and comfort.
Aerospace Industry
From simple brackets to complete rocket exhausts, DMLS parts are integral to commercial aircraft and rockets. Its ability to produce lightweight, strong components is essential in aerospace, where material performance and weight savings are crucial.
Which Additive Manufacturing Technique Should You Choose?
Selecting the right additive manufacturing technique depends heavily on the part’s intended function and application. Techniques like Electron Beam Melting (EBM) and Direct Metal Laser Sintering (DMLS) offer unmatched design freedom, recyclability, and production efficiency compared to traditional methods. However, with so many additive manufacturing options available, finding the best solution can be challenging.
At Alpha Precision Group, our team of experts is here to guide you. We take the time to understand your unique requirements and match you with the most effective and efficient manufacturing process for your application. Partner with us, and let’s bring your next project to life with precision and expertise.