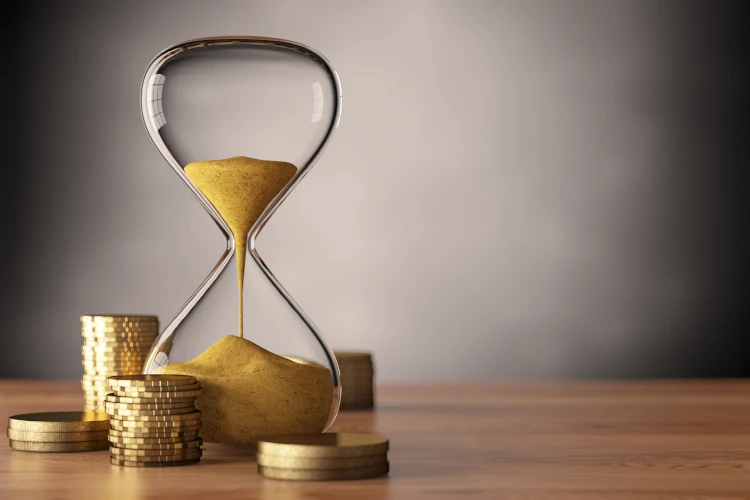
How can Metal Additive Manufacturing Shorten Time to Market?
If you’ve been following metal additive manufacturing (MAM), you probably already know about the many advantages the method offers over traditional manufacturing methods – this can include everything from increased flexibility of design, waste reduction, cost effectiveness (and the list goes on) – but did you know that it can also shorten time to market?
Here, we outline ways MAM can help deliver your part into the hands of your customers, including:
- Product development acceleration
- Capability for on-demand customization
- Testing parts before full production
- Hybrid additive manufacturing
Improving Time to Market with Metal AM
Below are just some of the ways metal AM can shorten time to market:
Product Development Acceleration
By using metal additive manufacturing, you can easily go from a CAD file to a functioning prototype, many times in less than a week, depending on size, AM technology used, etc. Additionally, you can easily manipulate the design as needed and reprint, unlike traditional PM, where you may need additional tooling/molds, which takes time. Lastly, a team of members from basically anywhere in the world can easily go into the CAD file and collaborate on needed changes – this can save on travel time, etc.
On-Demand Customization
With metal AM, you can think of a design today and print it by tomorrow. Not only can you think of one design, you can vet out multiple designs in one build box.
This can be particularly useful in the medical industry with patient-specific medical devices. Some jewelry designers are even using the technology to create custom pieces.
Test parts before full-production
Imagine you’re a firearm manufacturer and your customer has a design idea they’d like to test out. You could either use a different metal manufacturing process – which may take weeks or months to come to fruition – or you could leverage MAM as a bridge to production.
Rapid prototyping with metal AM allows you to quickly print a limited production run of parts that clients can touch, feel, and fire. This way, changes can easily be made, if desired, without adding a significant amount of time to the conceptualization process.
Hybrid Additive Manufacturing
MAM and traditional manufacturing processes don’t necessarily have to compete. In fact, they can work together to create complex, lightweight components, with excellent surface finish.
Hybrid additive manufacturing combines both additive and subtractive processes to create the desired component. Combining the two methods may be beneficial in instances where the main benefits of MAM are desired, though a smoother surface finish is needed. In these instances, hybrid manufacturing could combine the speed, efficiency and freedom of design of metal AM along with the surface control of CNC machining.
Are You Ready to Leverage the Benefits of Metal Additive Manufacturing?
If you find any of the above ideas intriguing, metal additive manufacturing may be an option for your next project.
Remember, it’s important to work closely with a partner who’s well-versed in metal additive manufacturing as well as traditional manufacturing methods to help you decide which options will work best for your component – this can depend on desired volume, speed, desired design flexibility, desired materials, and many other factors.
To learn more about metal additive manufacturing and what it may be able to do for your production, check out our resources.