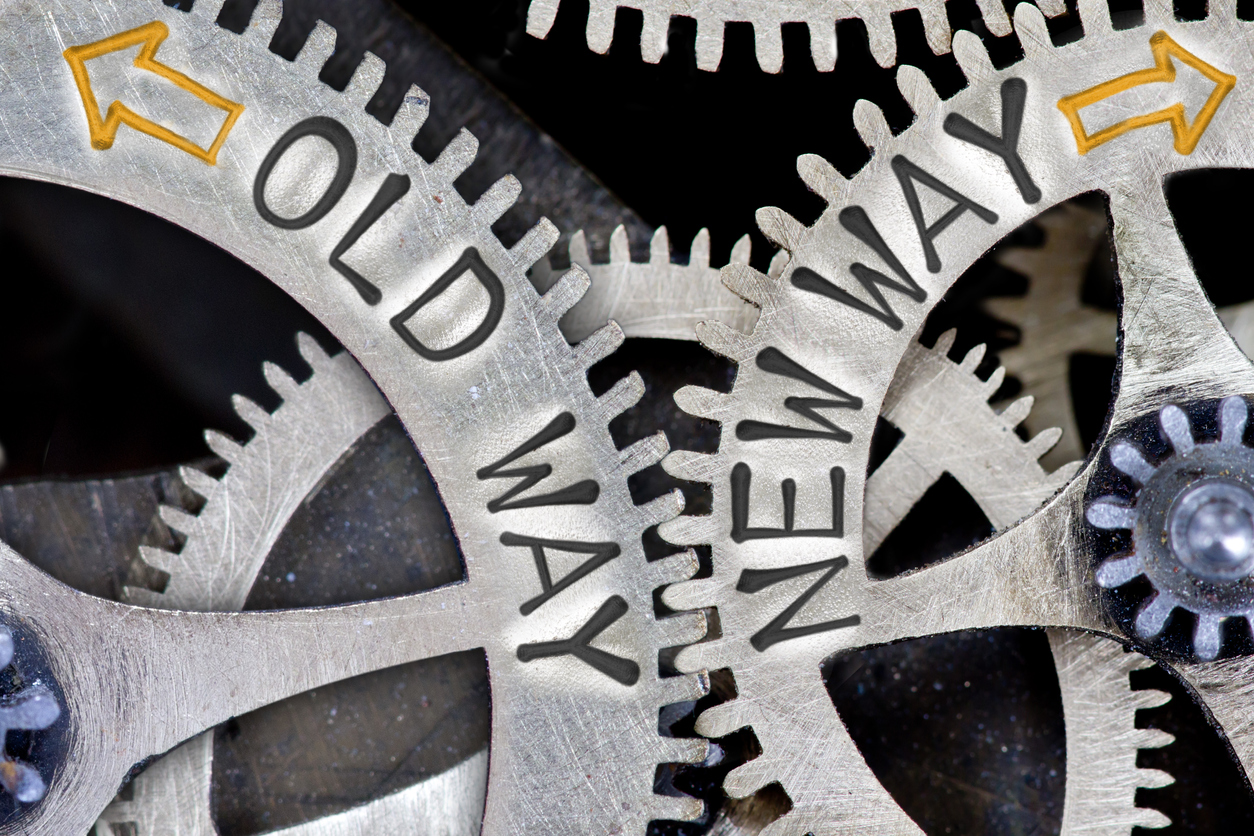
Metal Injection Molding vs. Metal Additive Manufacturing: A Comparison
Produce metal powder. Compact, then sinter.
For decades, metal manufacturing only consisted of those three steps. Now, the ways to produce with metal are nearly endless.
Two methods are frequently compared – metal injection molding (MIM) and metal additive manufacturing (MAM).
In this article, we’ll discuss the ins and outs of the processes, as well as determine when MIM is best, versus MAM.
Back to the Basics of MIM & MAM
Before we dive into which process is best, we’ll review the ins and outs of MIM and MAM.
First, what is metal injection molding?
Metal injection molding combines the design flexibility of plastic injection molding with the strength and durability of metal to create small components with tight tolerances.
The metal injection molding process comprises four steps:
- Preparing the feedstock by mixing metal powder with binders
- Injecting the feedstock into the mold cavity
- Removing most of the binder through debinding
- Sintering in a high-heat furnace to determine the part’s final properties
Metal injection molding is widely used not only because of the design flexibility and strength but also because it can create complex parts and handle large production runs.
Next, what is metal additive manufacturing?
Metal additive manufacturing, also known as metal 3D printing & metal AM, uses 3D scans or CAD files to build three-dimensional parts, layer-by-layer. Metal AM adds material repeatedly until the final component is created.
During the past decade, metal additive manufacturing has become the manufacturer’s choice for production due to its ability to mass-produce complex parts and shorten time-to-market.
Metal Injection Molding vs. Metal Additive Manufacturing
Now that we know the basics of both processes, let’s look at the three main differences between MIM and MAM:
- Production volume
- Lead times
- Post-processing
1. Production Volume
When producing with either method, mass production is cost-effective and efficient. However, if you’re looking to produce in low volume with rapid prototyping, metal additive manufacturing is the way to go.
Why would you want to produce in small quantities?
In some cases, rapid prototyping is necessary.
Instead of waiting months for prototype parts through other manufacturing methods, metal additive manufacturing is able to print a prototype in a few days, without significantly raising costs.
Since metal injection molding tooling, equipment, and set-up expenses add up quickly, when only producing in small quantities, the cost per unit can greatly increase.
2. Lead Times
If producing quickly is necessary, MIM may not be the best option. Metal injection molding tooling not only affects costs – it also lengthens time-to-market.
MIM tooling is part-specific. If you’re looking to design a new component shape, you’ll need a new mold, as well as a binder fixture. Creating this new tooling can take several weeks or months. Keep in mind, if the design is slightly off, the tooling production will start all over again.
On the other hand, metal additive manufacturing is able to switch designs quickly in CAD files and produce in large quantities, shortening lead times.
3. Post-Processing
As mentioned above, the final step in the metal injection molding process is sintering. After this step, the part is usable without any finishing required.
On the other hand, post-processing with metal additive manufacturing is essential.
In this step, the part is sanded, colored, cleaned, polished, or a combination of all of these.
While tooling isn’t required in the 3D printing process, it may be needed for post-processing. As a result, this final step can be more expensive than the printing itself.
Which Process is Best?
Unfortunately, the answer isn’t a straightforward one. It all depends on the project, its quantity and complexity, and many other factors.
When is MAM Right for the Job?
If you’re debating on metal additive manufacturing versus metal injection molding, but still aren’t sure, consider:
- Are you looking to shorten time-to-market?
- Do you want to create a complex component?
- Are you thinking about testing and switching designs?
- Will your product be produced in low volume?
If you answered “yes” to any of these questions, metal additive manufacturing could improve your production.
When is MIM Right for the Job?
In some cases, metal additive manufacturing isn’t the preferred method, even though it’s the latest technology. Sometimes, MIM is best. Like when considering MAM, ask yourself:
- Are your parts small and produced in large quantities?
- Do you need to be able to achieve tight tolerances?
- Are you looking to remove finishing processes?
- Do you plan on keeping one design for your component?
If your answer was “yes” to any questions in the list, metal injection molding may be a process that would work for your manufacturing.
The Final Decision
Deciding between metal injection molding vs. metal additive manufacturing isn’t an easy decision. When you take the many factors into consideration, it can get confusing.
Remember: MIM may be the best choice for high-volume, repeatable manufacturing of small parts.
On the other hand, if you’re producing at high or low volumes, changing designs, and looking for complexity, MAM may be the way to go.
Getting Started in Metal Part Fabrication
If you’re still unsure about the best process for your project, reach out to our team of knowledgeable metal experts.