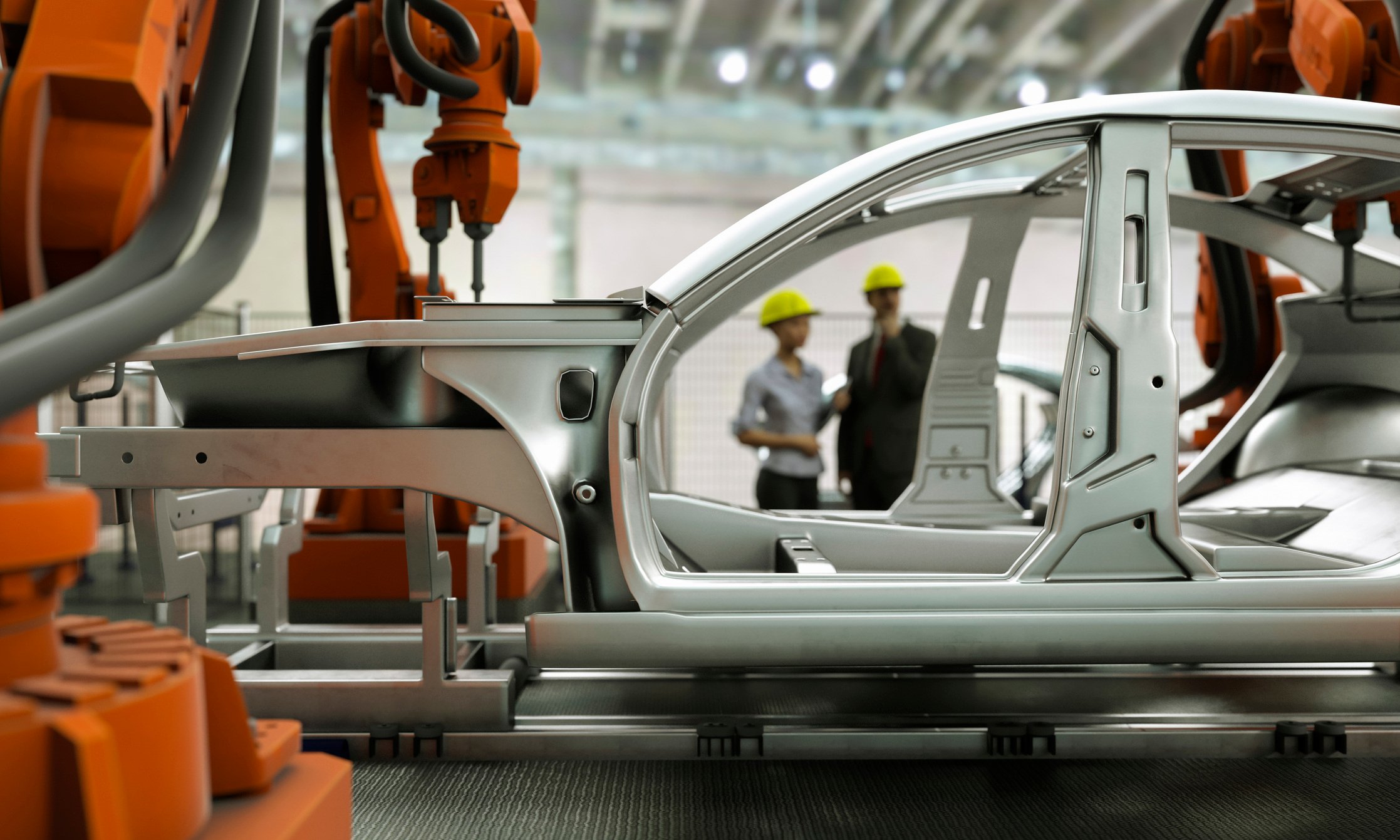
Metal 3D Printing: Rapid Prototyping in the Automotive Industry
Rapid prototyping in the automotive industry is like fine-tuning a high-performance engine—both require precision, innovation, and timely adjustments to achieve peak performance. As manufacturers face shifting market demands and seek breakthrough innovations, so do the challenges and opportunities of rapid prototyping.
Rapid prototyping with metal 3D printing allows quicker design iterations, reducing time from concept to production. The benefits are clear: faster innovation cycles, reduced waste, and improved resource capability.
This article will delve into:
- The role of rapid prototyping in accelerating automotive innovation
- Challenges presented in the industry where rapid prototyping helps
- The impact of 3D printing in the automotive industry
- Successful case stories using 3D printing in the industry
Designing the Future: Rapid Prototyping in the Automotive Industry
Rapid prototyping has become an important part of the automotive industry, improving innovation and efficiency in vehicle design and manufacturing. This approach allows engineers and designers:
- Shortening lead times
- Quicker design changes
Shortening Lead Times
Unlike traditional manufacturing processes that often require extensive setups and longer lead times, 3D printing allows for on-demand production, helping manufacturers quickly adapt to changing market demands and consumer preferences. This flexibility is particularly beneficial in creating custom parts or limited runs of specialized vehicles, as production can be scaled up or down easily. Furthermore, the ability to refine designs rapidly encourages innovation, allowing companies to explore new ideas without the constraints of conventional manufacturing. This allows automotive manufacturers to quickly adapt to market changes and cut waste, using resources better. This shift redefines how vehicles are designed and produced, laying the groundwork for a more responsive and efficient automotive landscape.
Quick Design Changes
By using advanced technologies such as 3D printing and computer-aided design, companies can gather invaluable feedback early in the development cycle, reducing the risk of costly errors later. Additionally, rapid prototyping promotes collaboration among cross-functional teams, encouraging a culture of creativity and problem-solving, which is needed to meet the fast-paced demands of modern automotive consumers. Ultimately, incorporating rapid prototyping into the automotive industry speeds up the time-to-market for new vehicles and improves the final product quality and performance.
Are you curious about what more there is to learn about AM in the Automotive industry?
Read on in our blog here
Addressing The Challenges Presented in the Industry Where Rapid Prototyping Helps
In the automotive industry, three main key challenges can delay design and manufacturing processes, where rapid prototyping through technologies like 3D printing offers practical solutions. These three significant challenges include:
- Long lead times
- High costs associated with traditional methods
- Delayed risk of costly design flaws
- Slow speed-to-market
Long Lead Times
One of the primary issues is the long lead times associated with traditional manufacturing, which can delay the time to market for new vehicles. Rapid prototyping allows teams to produce prototypes, repeat the use, and refine the designs quickly to reduce these lead times considerably.
Tooling, which includes the creation of molds and fixtures necessary for manufacturing components, requires a significant investment. Due to extensive design and machining processes, traditional tooling methods can require substantial time and financial resources. This high cost can be challenging for smaller manufacturers’ budgets or those looking to innovate with new designs. Rapid prototyping through 3D printing addresses this issue by allowing manufacturers to create tooling components quickly and cost-effectively, reducing lead times and capital expenditure. This flexibility reduces lead times significantly, as there is no need to wait for molds or other tooling to be manufactured. Additionally, the cost-effectiveness of 3D printing reduces capital expenditure by eliminating the need for expensive tooling equipment and materials, making it affordable to produce complex designs without the financial burden typically associated with traditional manufacturing processes.
High Costs Associated with Traditional Methods
Developing and producing prototypes using traditional methods can be restrictive, particularly for startups and smaller manufacturers. 3D printing significantly cuts costs and allows for more budget-friendly experimentation by helping the production of inexpensive, low-volume parts.
Reducing production costs is one of rapid prototyping's most significant impacts on the automotive industry. Metal 3D printing allows for additive manufacturing, where parts are built layer by layer, reducing waste only by using the required material. This process lowers material costs and reduces the total resources needed for production, making it more economically reasonable for manufacturers.
Delayed Risk of Costly Design Flaws
Rapid prototyping in the automotive industry helps identify design flaws early in development, reducing the risk of costly errors in full-scale production. This strategic technique enables efficiency, product quality, and alignment with market expectations.
Designers are no longer restricted by the limitations of traditional manufacturing techniques, which often limit various geometries and complexity. Instead, they can create complex designs that optimize strength-to-weight ratios, improve aerodynamics, and improve overall vehicle performance. This flexibility allows the production of unique components that can improve functionality and aesthetics.
Furthermore, streamlined assembly is another advantage offered by metal 3D printing. Complex assemblies can be produced into a single part, limiting the number of components needed and the time required for assembling. This streamlined approach saves production time and can improve the final product's reliability.
The customization options also allow manufacturers to create custom components tailored to specific customer requirements. This capability benefits luxury automotive markets, where unique designs are a key selling point.
Slow Speed to Market
Lastly, the speed to market is greatly improved, as metal 3D printing drastically decreases production timelines. With the ability to quickly produce prototype designs for testing, manufacturers can make timely adjustments, improve their products, and respond to market demands more effectively than ever. Overall, metal 3D printing is industry-changing in the automotive sector, paving the way for innovative design and more efficient production processes.
Read more here about Metal 3D Printing in Motion
Your Metal 3D Printing Strategy: Beyond Just Speed
Rapid prototyping with metal 3D printing allows you to adjust and refine designs quickly and strategically sets your operations apart. It’s not just about doing things faster than your competitors but with a unique precision and flexibility that only this technology can offer. Innovate and customize components in previously impossible ways, creating value that's uniquely yours.
Need Expert Guidance on Integrating 3D Printing into Your Production Line?
At Alpha Precision Group, we have decades of experience helping businesses tailor their production capabilities with the latest technologies. Request your consultation today and discover how metal 3D printing can improve your automotive prototyping, efficiency, and innovation in your operations.