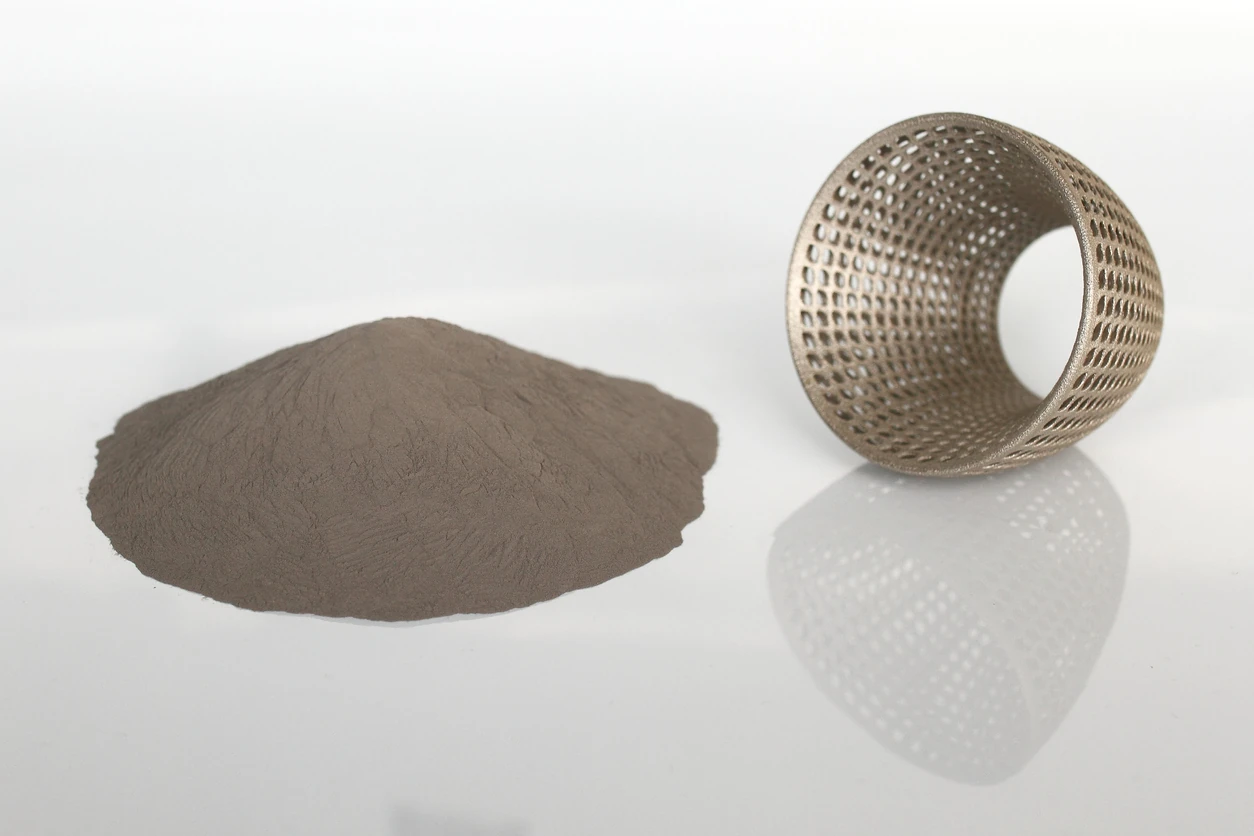
Metal Binder Jetting vs Other Metal Additive Manufacturing Processes
Metal additive manufacturing is a swiftly growing technology that can produce complex components with a high degree of design freedom for engineers. Once solely promoted for rapid prototyping, many metal additive manufacturing machines can now produce strong and reliable end-use parts.
While there are a wide variety of additive manufacturing processes available, today we’ll focus on methods that are most compatible with metals, starting with an overview of the metal binder jetting process.
Metal Binder Jetting
How it works: During the metal binder jetting process, a binding agent (usually a liquid) serves as an adhesive between layers of powder. A print head moves horizontally along the x and y axes of the machine, depositing layers on the build platform, binding the material.
Common applications for binder jetting include:
- Rapid to fully functional prototypes
- Rapid tooling, fixtures, and jigs
- Dense and durable metals used in metal binder jetting make it ideal for end-use products
Advantages of Metal Binder Jetting
Binder jetting has a lot of advantages over other metal manufacturing processes, both additive and subtractive, including:
- Printing supports aren’t always needed, which cuts down on material and post-processing time
- Binder jet systems can recycle and reuse up to 99% of loose powder
- Enables engineers to produce complex designs without increasing costs
- Can produce multiple parts in one print, reducing costs and development time
- Manufactured parts are isotropic, meaning they’re equally strong in all directions
- The technology is rapidly advancing, enabling the production of larger parts and opening paths to a wider range of material options
Disadvantages of Metal Binder Jetting
While there are many advantages of this type of metal additive manufacturing, no process is perfect. Drawbacks of metal binder jetting include:
- Requires additional equipment for post processing
- Most post-print processes are manual, though development is underway to automate
- Equipment costs are greater than that of subtractive manufacturing techniques
Powder Bed Fusion
How it works: The powder bed fusion process includes several printing methods, including electron beam melting (EBM), direct metal laser sintering (DMLS), selective laser sintering (SLS), selective laser melting (SLM), and selective heat sintering (SHS). Ultimately, powder bed fusion uses lasers or electron beams to melt and fuse different powder materials.
Common applications of powder bed fusion include:
- End use parts for automotive, aerospace and other industries
- Fabrication of jigs and fixtures
- Orthotics and prosthetics
- Automation and end-of-arm tooling
- Molds and investment casting
Advantages of Powder Bed Fusion
Powder bed fusion has some of the same advantages as metal binder jetting, including:
- Minimal supports are usually needed because the powder acts as an integrated support structure
- Excess powder can be recycled
Disadvantages of Powder Bed Fusion
As with all additive manufacturing processes, powder bed fusion also has its disadvantages:
- Powder preheating, vacuum generation, and cooling off periods add to the build time, making it one of the slowest additive manufacturing techniques
- Post-processing steps can lead to increased production time and cost
- Quality of the surface depends on the grain size of the powder and is similar to processes like sand casting, etc.
Material Extrusion
How it works: During the material extrusion process, material is drawn through a nozzle, heated, and deposited onto the build platform, layer by layer. The nozzle moves horizontally, while the platform moves up and down as each layer is deposited.
Originally used with plastics and polymers, metals have been added to the list of materials compatible with material extrusion in recent years.
Metal material extrusion is most compatible with rapid prototyping.
Advantages of Material Extrusion
Advantages of the metal material extrusion include:
- Can create rapid prototypes for a very low cost, compared to other additive manufacturing processes
- Prints have high precision with fine layers
Disadvantages of Material Extrusion
While material extrusion is excellent for rapid prototyping, there are several downfalls of this type of additive manufacturing:
- Limited production potential: Manufacturing process tends to leave small voids and bubbles in parts, resulting from the melted material leaving the nozzle as it’s applied in different directions - this can have an impact on final part properties and porosity
- High binder content makes sintering difficult
- Parts manufactured this way are lower in density than those created with traditional metal manufacturing processes
- More supports may be required than other metal additive manufacturing processes, such as binder jetting or powder bed fusion
Which Method Will You Choose?
As you can see, each process has strengths and weaknesses. Ultimately the metal additive manufacturing technology you choose will depend on what you want to produce and material you want to use.
Ready to learn more? Check out our blog for more metal additive manufacturing resources.