Guide to Metal Additive Manufacturing For Medical
Unleash the Power of Precision, Customization, & Innovation
The medical industry is evolving rapidly, and traditional manufacturing methods struggle to keep up with the demand for cutting-edge, patient-specific solutions. Metal additive manufacturing (AM) is changing the game—allowing engineers and manufacturers to design and produce complex medical devices with unprecedented precision, speed, and efficiency.
In this guide, we’ll explore the benefits of metal additive manufacturing in the medical industry and technical & quality control considerations.
In a hurry but still want to read? Download the eBook and take it with you!
Benefits of Metal Additive Manufacturing in the Medical Industry
In the fast-paced world of medical device manufacturing, engineers and decision-makers face a constant challenge: how to balance the need for precision, customization, and innovation with the realities of cost, time-to-market, and regulatory compliance.
Traditional manufacturing methods, while reliable, often need help to keep up with the demands of today's healthcare landscape. This is where medical additive manufacturing (AM) comes in – a transformative technology changing how medical devices are designed, produced, and delivered.
By enabling the creation of complex, patient-specific parts on demand, AM empowers engineers to push the boundaries of what's possible, leading to a multitude of advantages.
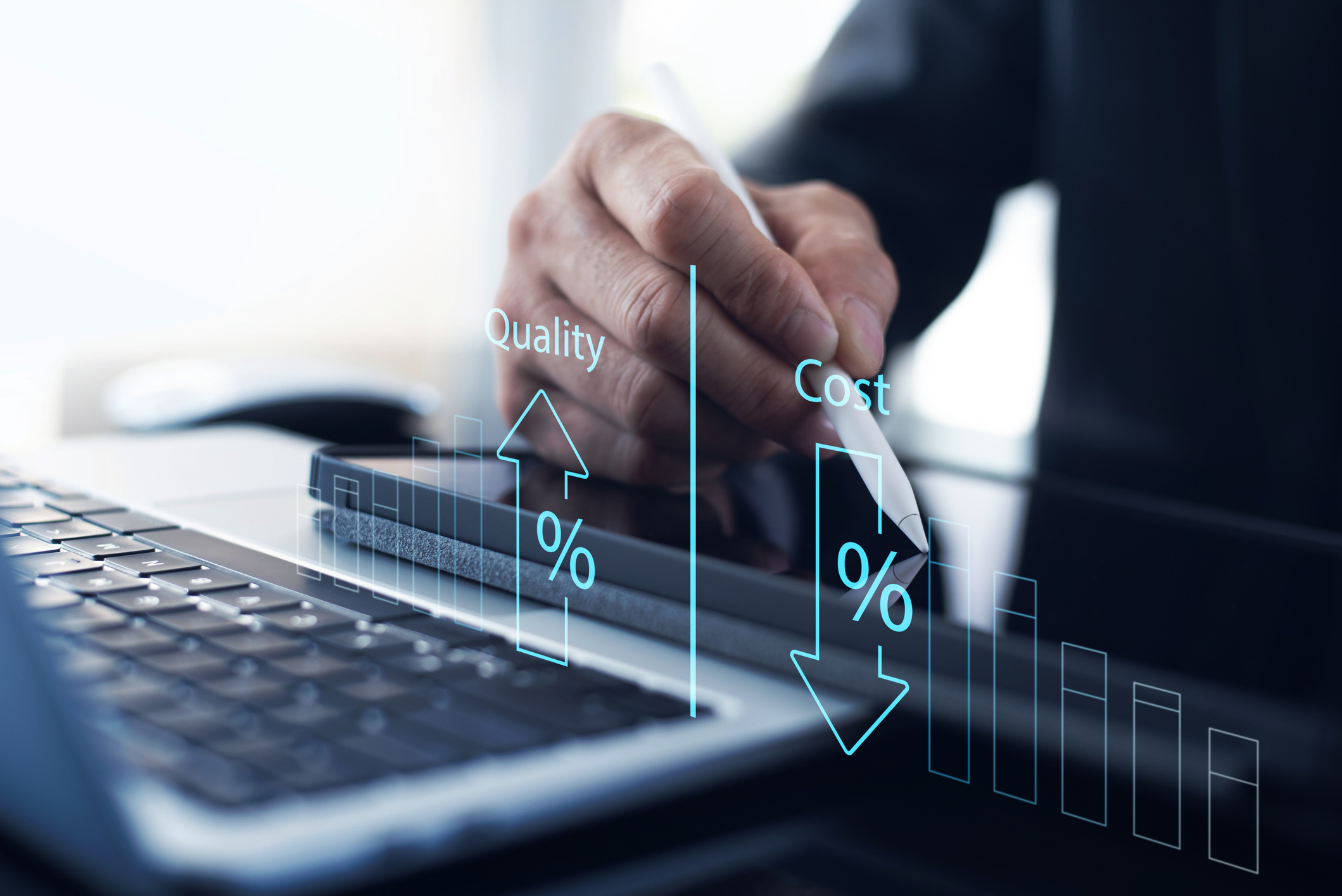
1. Reduction of Product Development Cost/Waste
Unlike traditional subtractive manufacturing methods that involve material removal and often result in waste, additive manufacturing builds parts layer by layer, minimizing material use and reducing costs. Additionally, techniques like lightweighting can further optimize material consumption, leading to even greater cost savings
2. On-Demand Manufacturing
Say goodbye to lengthy tooling processes that delay product development for weeks or months. With additive manufacturing, 3D printing of medical instruments and devices can begin immediately after the design is finalized, enabling rapid prototyping and faster iteration cycles. This allows you to get your products to market sooner, respond quickly to changing customer needs, and even produce customized devices on demand.
3. Part Consolidation/Complex Parts
Additive manufacturing empowers engineers with unprecedented design freedom. Complex geometries and intricate features that were once impossible or prohibitively expensive to manufacture using traditional methods are now readily achievable. This allows for part consolidation, reducing assembly time and complexity, and minimizing the risk of errors.
4. High Level of Customization
Patient-specific devices are no longer a distant dream. Additive manufacturing allows for easy modification of 3D design files, eliminating the need for costly custom molds and tooling. This enables the creation of personalized implants, prosthetics, and surgical tools that perfectly match the patient's anatomy and needs, leading to improved outcomes and increased patient satisfaction.
Technical Considerations in Metal Additive Manufacturing
While additive manufacturing offers numerous benefits, there are several technical considerations that you should keep in mind when implementing this technology for medical device production:
1. Biocompatible Materials
Choosing the right materials is critical to ensuring patient safety and the longevity of implants and prosthetics. Commonly used biocompatible metals include:
- Titanium and its alloys: Titanium is renowned for its excellent strength-to-weight ratio, superior corrosion resistance, and biocompatibility. It also promotes osseointegration, making it an ideal choice for orthopedic implants.
- Stainless steel: Although not typically used for implants due to lower biocompatibility, stainless steel offers strength and corrosion resistance at a more affordable price point. It is often used for surgical tools and other medical devices.
- Cobalt-chrome alloys: These alloys surpass titanium and stainless steel in terms of strength and wear resistance, making them suitable for high-stress applications like knee and hip replacements. However, their stiffness can lead to stress shielding, which may affect long-term implant performance.
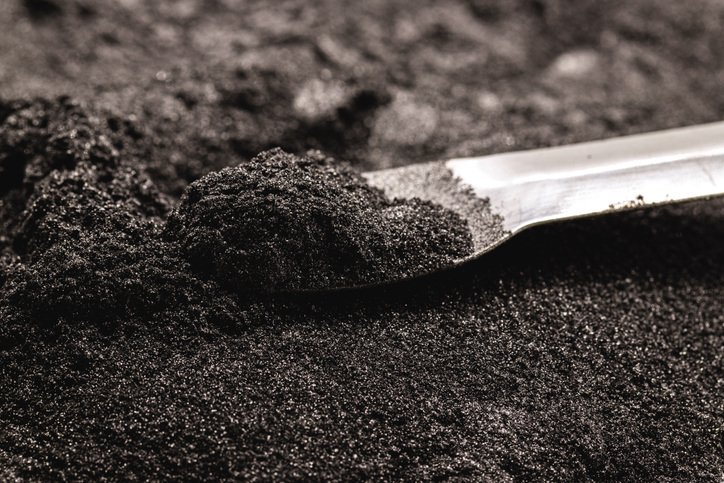
Material | Pros | Cons | Common Applications |
Titanium |
Excellent strength-to-weight ratio, superior corrosion resistance, biocompatible, promotes osseointegration | Relatively expensive |
Orthopedic implants, dental implants, surgical instruments |
Stainless Steel |
Strong, corrosion-resistant, affordable |
Lower biocompatibility, potential for ion release |
Surgical tools, medical device components |
Cobalt-Chrome Alloys |
High strength, wear-resistant, suitable for high-stress applications |
Stiffness can lead to stress shielding |
Knee and hip replacements, dental implants |
2. Design for Additive Manufacturing (DfAM)
To fully leverage the capabilities of additive manufacturing, you should adopt a Design for Additive Manufacturing (DfAM) approach. This involves optimizing designs for printability, incorporating features like lattices and internal channels, and considering factors like support structures and build orientation. DfAM enables the creation of highly complex, patient-specific devices that enhance functionality and improve patient outcomes.
3. Bone Scaffold 3D Printing
Additive manufacturing plays a crucial role in the development of bone scaffolds, which are used to promote bone tissue regeneration. Key considerations in bone scaffold design include:
- Pore size and porosity: The scaffold's porosity must be carefully balanced to allow for cell infiltration and vascularization while maintaining adequate mechanical strength.
- Structure for osseointegration: The scaffold's architecture should promote the formation of new bone tissue and its integration with the existing bone.
- Material strength: The chosen material must possess sufficient mechanical strength to support the surrounding bone structure during the healing process.
4. Surface Finish and Post-Processing
The surface finish of medical implants directly impacts their biocompatibility, tissue integration, and risk of infection. Post-processing techniques like polishing, cleaning, and surface treatments ensure optimal surface quality and minimize complications.
Quality Control & Additive Manufacturing
In metal additive manufacturing, stringent quality control measures are essential to maintain product integrity and meet regulatory requirements.
The Importance of Quality Control
MAM involves intricate processes that demand meticulous attention to detail. From powder quality and machine calibration to build parameters and post-processing, every step can affect the final product's performance. Robust quality control protocols are crucial to identify and mitigate potential defects, ensuring that medical devices produced through MAM meet the highest standards of safety and reliability.
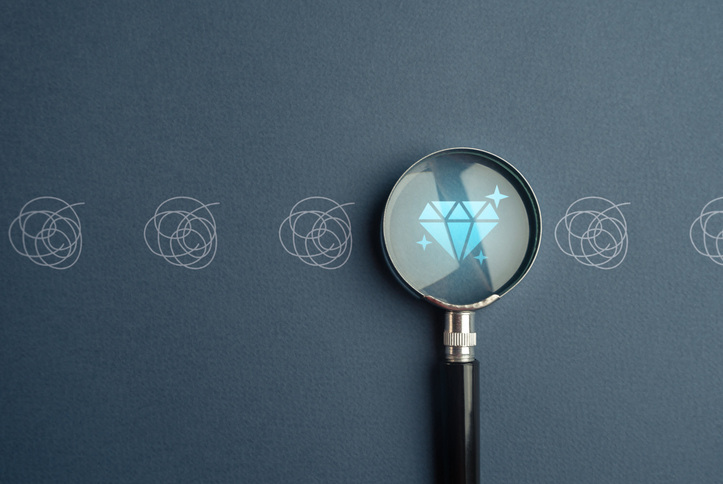
Advanced Quality Control Methods
Various quality control methods are employed in MAM, including:
- Six Sigma: A data-driven methodology focused on minimizing defects and process variability.
- Statistical Process Control (SPC): Involves monitoring and controlling manufacturing processes using statistical analysis to detect and prevent deviations.
- Failure Mode and Effects Analysis (FMEA): A proactive approach to identify potential failure modes and their effects, allowing for preventive action.
These advanced methods, combined with rigorous testing and inspection, help maintain product integrity throughout the MAM process, fostering confidence in the safety and performance of medical devices.
The Impact of Medical Additive Manufacturing on Healthcare
Metal additive manufacturing is not just a manufacturing technology; it's a catalyst for transformation in the healthcare industry. Its ability to create highly personalized, precise, and efficient medical devices, implants, and tools reshapes healthcare delivery.
Accelerating Innovation with Rapid Prototyping
Rapid prototyping, enabled by MAM, empowers engineers and designers to iterate quickly, test new ideas, and bring innovative medical solutions to market faster than ever before. This accelerates innovation, leading to advancements in patient care and improved treatment options.
Reducing Waste and Costs
Traditional manufacturing methods often involve significant material waste and high production costs. MAM minimizes waste and optimizes resource utilization, translating into cost savings that can be passed on to patients and healthcare providers.
Enhancing Patient Care
MAM allows for the creation of custom-fit implants and surgical tools that perfectly match the patient's anatomy and needs. This personalized approach improves surgical outcomes, reduces recovery times, and enhances patient satisfaction. From orthopedic implants to dental restorations, MAM is making healthcare more personalized and effective.
Pushing Innovation in Medical Manufacturing with Metal AM
Medical additive manufacturing represents a paradigm shift in the medical device industry, offering unprecedented precision, customization, and innovation. From cost reduction and rapid prototyping to enhanced patient care and accelerated innovation, the benefits of AM are undeniable.
As you navigate the complexities of medical device manufacturing, consider the transformative potential of additive manufacturing. Embrace this technology to unlock new possibilities, drive innovation, and ultimately, improve the lives of patients around the world.
Ready to Take the Next Step?
Contact us today to explore how medical additive manufacturing can transform your product development process and help you deliver innovative, patient-centric solutions.